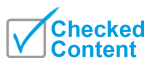
Pottery
Did you know...
SOS Children have produced a selection of wikipedia articles for schools since 2005. Do you want to know about sponsoring? See www.sponsorachild.org.uk


Pottery is the material from which the potteryware is made, of which major types include earthenware, stoneware and porcelain. The place where such wares are made is also called a pottery (plural "potteries"). Pottery also refers to the art or craft of the potter or the manufacture of pottery.
The definition of pottery used by ASTM is "all fired ceramic wares that contain clay when formed, except technical, structural, and refractory products." Some archaeologists use a different understanding by excluding ceramic objects such as figurines which are made by similar processes, materials and the same people but are not vessels.
Background
Pottery is made by forming a clay body into objects of a required shape and heating them to high temperatures in a kiln which removes all the water from the clay, which induces reactions that lead to permanent changes including increasing their strength and hardening and setting their shape. A clay body can be decorated before or after firing. Prior to some shaping processes, clay must be prepared. Kneading helps to ensure an even moisture content throughout the body. Air trapped within the clay body needs to be removed. This is called de-airing and can be accomplished by a machine called a vacuum pug or manually by wedging. Wedging can also help produce an even moisture content. Once a clay body has been kneaded and de-aired or wedged, it is shaped by a variety of techniques. After shaping it is dried and then fired.
Physical stages of clay
Clay ware takes on varying physical characteristics during the making of pottery.
- Greenware refers to unfired objects. Clay bodies at this stage are in their most plastic form. They are soft and malleable. Hence they can be easily deformed by handling.
- Leather-hard refers to a clay body that has been dried partially. At this stage the clay object has approximately 15% moisture content. Clay bodies at this stage are very firm and only slightly pliable. Trimming and handle attachment often occurs at the leather-hard state.
- Bone-dry refers to clay bodies when they reach a moisture content at or near 0%. It is now ready to be bisque fired.
- Bisque (pottery) refers to the clay after the object is shaped to the desired form and fired in the kiln for the first time, known as "bisque fired". This firing changes the clay body in several ways. Mineral components of the clay body will undergo chemical changes that will change the colour of the clay.
- Glaze fired is the final stage of some pottery making. A glaze may be applied to the bisque form and the object can be decorated in several ways. After this the object is "glazed fired", which causes the glaze material to melt, then adhere to the object. The glaze firing will also harden the body still more as chemical processes can continue to occur in the body.
Clays and mineral contents
There are several materials that are referred to as clay. The properties of the clays differ in: Plasticity, the malleability of the body; porosity, the degree to which the fired pottery will absorb water; and shrinkage, the degree of reduction in size of a body as water is removed. The various clays also differ in the way in which they respond to different degrees of heat when fired in the kiln. A clay body can be decorated before or after firing. Prior to some shaping processes, clay must be prepared. Each of these different clays are composed of different types and amounts of minerals that determine the resulting pottery. There are wide regional variations in the properties of raw materials used for the production of pottery, and this can lead to wares that are unique in character to a locality. It is common for clays and other materials to be mixed to produce clay bodies suited to specific purposes. The two essential components of clay are Silica and Alumina which combine to form Aluminium silicate, also known as Kaolinite. Other mineral compounds in the clay may act as Fluxes to lower the melting point of the silica during firing. Following is a list of different types of clay used for pottery that are available in different regions of the world.
- Kaolin, is sometimes referred to as China clay because it was first identified in China.
- Ball clay An extremely plastic, fine grained sedimentary clay, which may contain some organic matter. It is usually added to porcelain to increase plasticity.
- Fire clay A clay having a slightly higher percentage of fluxes than Kaolin, but usually quite plastic. It is highly heat resistant form of clay which can be combined with other clays to increase the firing temperature and may be used as an ingredient to make stoneware type bodies.
- Stoneware clay Suitable for creating Stoneware. This clay has many of the characteristics between fire clay and ball clay, having finer grain, like ball clay but more heat resistant like fire clays.
- Common red clay and Shale clay have vegetable and Ferric oxide impurities which make them useful for bricks, but are generally unsatisfactory for pottery except under special conditions of a particular deposit.
- Bentonite An extremely plastic clay which can be added in small quantities to short clay to make it more plastic.
Methods of shaping

Pottery can be shaped by a range of methods that include:

Hand building. This is the earliest forming method. Wares can be constructed by hand from coils of clay, combining flat slabs of clay, or pinching solid balls of clay or some combination of these. Parts of hand-built vessels are often joined together with the aid of slip, an aqueous suspension of clay body and water. A clay body can be decorated before or after firing. Prior to some shaping processes, clay must be prepared such as tablewares although some studio potters find hand-building more conducive to create one-of-a-kind works of art.

The potter's wheel. In a process called "throwing" (coming from the Old English word thrawan which means to twist or turn, a ball of clay is placed in the centre of a turntable, called the wheel-head, which the potter rotates with a stick, with foot power or with a variable-speed electric motor.
During the process of throwing, the wheel rotates rapidly while the solid ball of soft clay is pressed, squeezed and pulled gently upwards and outwards into a hollow shape. The first step of pressing the rough ball of clay downward and inward into perfect rotational symmetry is called centring the clay—a most important skill to master before the next steps: opening (making a centred hollow into the solid ball of clay), flooring (making the flat or rounded bottom inside the pot), throwing or pulling (drawing up and shaping the walls to an even thickness), and trimming or turning (removing excess clay to refine the shape or to create a foot).
Considerable skill and experience are required to throw pots of an acceptable standard and, while the ware may have high artistic merit, the reproducibility of the method is poor. Because of its inherent limitations, throwing can only be used to create wares with radial symmetry on a vertical axis. These can then be altered by impressing, bulging, carving, fluting, and incising. In addition to the potter's hands these techniques can use tools, including paddles, anvils & ribs, and those specifically for cutting or piercing such as knives, fluting tools and wires. Thrown pieces can be further modified by the attachment of handles, lids, feet and spouts.
Granulate pressing: As the name suggests, this is the operation of shaping pottery by pressing clay in a semi-dry and granulated condition in a mould. The clay is pressed into the mould by a porous die through which water is pumped at high pressure. The granulated clay is prepared by spray-drying to produce a fine and free-flowing material having a moisture content of between about 5 and 6 per cent. Granulate pressing, also known as dust pressing, is widely used in the manufacture of ceramic tiles and, increasingly, of plates.
Injection moulding: is a shape-forming process adapted for the tableware industry from the method long established for the forming of thermoplastic and some metal components. It has been called Porcelain Injection Moulding, or PIM. Suited to the mass production of complex-shaped articles, one significant advantage of the technique is that it allows the production of a cup, including the handle, in a single process, and thereby eliminates the handle-fixing operation and produces a stronger bond between cup and handle. The feed to the mould die is a mix of approximately 50 to 60 percent unfired body in powder form, together with 40 to 50 percent organic additives composed of binders, lubricants and plasticisers. The technique is not as widely used as other shaping methods.
Jiggering and jolleying: These operations are carried out on the potter's wheel and allow the time taken to bring wares to a standardized form to be reduced. Jiggering is the operation of bringing a shaped tool into contact with the plastic clay of a piece under construction, the piece itself being set on a rotating plaster mould on the wheel. The jigger tool shapes one face while the mould shapes the other. Jiggering is used only in the production of flat wares, such as plates, but a similar operation, jolleying, is used in the production of hollow-wares such as cups. Jiggering and jolleying have been used in the production of pottery since at least the 18th century. In large-scale factory production, jiggering and jolleying are usually automated, which allows the operations to be carried out by semi-skilled labour.
Roller-head machine: This machine is for shaping wares on a rotating mould, as in jiggering and jolleying, but with a rotary shaping tool replacing the fixed profile. The rotary shaping tool is a shallow cone having the same diameter as the ware being formed and shaped to the desired form of the back of the article being made. Wares may in this way be shaped, using relatively unskilled labour, in one operation at a rate of about twelve pieces per minute, though this varies with the size of the articles being produced. Developed in the U.K. just after World War II by the company Service Engineers, roller-heads were quickly adopted by manufacturers around the world; they remain the dominant method for producing flatware.
Pressure casting – specially developed polymeric materials allow a mould to be subject to application external pressures of up to 4.0 MPa–so much higher than slip casting in plaster moulds where the capillary forces correspond to a pressure of around 0.1 - 0.2 MPa. The high pressure leads to much faster casting rates and, hence, faster production cycles. Furthermore, the application of high pressure air through the polymeric moulds upon demoulding the cast means a new casting cycle can be started immediately in the same mould, unlike plaster moulds which require lengthy drying times. The polymeric materials have much greater durability than plaster and, therefore, it is possible to achieve shaped products with better dimensional tolerances and much longer mould life. Pressure casting was developed in the 1970s for the production of sanitaryware although, more recently, it has been applied to tableware.
RAM pressing: is used to shape ware by pressing a bat of prepared clay body into a required shape between two porous moulding plates. After pressing, compressed air is blown through the porous mould plates to release the shaped wares.
Slipcasting: is ideally suited to the making of wares that cannot be formed by other methods of shaping. A slip, made by mixing clay body with water, is poured into a highly absorbent plaster mould. Water from the slip is absorbed into the mould leaving a layer of clay body covering its internal surfaces and taking its internal shape. Excess slip is poured out of the mould, which is then split open and the moulded object removed. Slipcasting is widely used in the production of sanitary wares and is also used for making smaller articles, such as intricately detailed figurines.
Decorating and glazing
Pottery may be decorated in a number of ways including:
- In the clay body, for example, by incising patterns on its surface.
- Underglaze decoration (in the manner of many blue and white wares).
Underglaze may be applied by brush strokes, air brush, or by pouring the underglaze into the mold, covering the inside, creating a swirling effect, then the mold is filled with slip.
- In-glaze decoration
- On-glaze decoration
- Enamel
Additives can be worked into the clay body prior to forming, to produce desired effects in the fired wares. Coarse additives such as sand and grog (fired clay which has been finely ground) are sometimes used to give the final product a required texture. Contrasting coloured clays and grogs are sometimes used to produce patterns in the finished wares. Colourants, usually metal oxides and carbonates, are added singly or in combination to achieve a desired colour. Combustible particles can be mixed with the body or pressed into the surface to produce texture.
Agateware: Named after its resemblance to the quartz mineral agate which has bands or layers of colour that are blended together, agatewares are made by blending clays of differing colours together but not mixing them to the extent that they lose their individual identities. The wares have a distinctive veined or mottled appearance. The term "agateware" is used to describe such wares in the United Kingdom; in Japan the term "neriage" is used and in China, where such things have been made since at least the Tang Dynasty, they are called "marbled" wares. Great care is required in the selection of clays to be used for making agatewares as the clays used must have matching thermal movement characteristics.
Banding: This is the application by hand or by machine of a band of colour to the edge of a plate or cup. Also known as "lining", this operation is often carried out on a potter's wheel.
Burnishing: The surface of pottery wares may be burnished prior to firing by rubbing with a suitable instrument of wood, steel or stone to produce a polished finish that survives firing. It is possible to produce very highly polished wares when fine clays are used or when the polishing is carried out on wares that have been partially dried and contain little water, though wares in this condition are extremely fragile and the risk of breakage is high.

Engobe: This is a clay slip, that is used to coat the surface of pottery, usually before firing. Its purpose is often decorative though it can also be used to mask undesirable features in the clay to which it is applied. Engobe slip may be applied by painting or by dipping to provide a uniform, smooth, coating. Engobe has been used by potters from pre-historic times until the present day and is sometimes combined with sgraffito decoration, where a layer of engobe is scratched through to reveal the colour of the underlying clay. With care it is possible to apply a second coat of engobe of a different colour to the first and to incise decoration through the second coat to expose the colour of the underlying coat. Engobes used in this way often contain substantial amounts of silica, sometimes approaching the composition of a glaze.
Litho: This is a commonly used abbreviation for lithography, although the alternative names of transfer print or "decal" are also common. These are used to apply designs to articles. The litho comprises three layers: the colour, or image, layer which comprises the decorative design; the cover coat, a clear protective layer, which may incorporate a low-melting glass; and the backing paper on which the design is printed by screen printing or lithography. There are various methods of transferring the design while removing the backing-paper, some of which are suited to machine application.
Gold: Decoration with gold is used on some high quality ware. Different methods exist for its application, including:
- Best gold - a suspension of gold powder in essential oils mixed with a flux and a mercury salt extended. This can be applied by a painting technique. From the kiln, the decoration is dull and requires burnishing to reveal the full colour
- Acid Gold – a form of gold decoration developed in the early 1860s at the English factory of Mintons Ltd, Stoke-on-Trent. The glazed surface is etched with diluted hydrofluoric acid prior to application of the gold. The process demands great skill and is used for the decoration only of ware of the highest class.
- Bright Gold – consists of a solution of gold sulphoresinate together with other metal resonates and a flux. The name derives from the appearance of the decoration immediately after removal from the kiln as it requires no burnishing
- Mussel Gold – an old method of gold decoration. It was made by rubbing together gold leaf, sugar and salt, followed by washing to remove solubles
Glazing
Glaze is a glassy coating on pottery, the primary purposes of which are decoration and protection. One important use of glaze is to render porous pottery vessels impermeable to water and other liquids. Glaze may be applied by dusting the unfired composition over the ware or by spraying, dipping, trailing or brushing on a thin slurry composed of the unfired glaze and water. The colour of a glaze before it has been fired may be significantly different than afterwards. To prevent glazed wares sticking to kiln furniture during firing, either a small part of the object being fired (for example, the foot) is left unglazed or, alternatively, special refractory "spurs" are used as supports. These are removed and discarded after the firing.
Some specialised glazing techniques include:
- Salt-glazing, where common salt is introduced to the kiln during the firing process. The high temperatures cause the salt to volatize, depositing it on the surface of the ware to react with the body to form a sodium aluminosilicate glaze. In the 17th and 18th centuries, salt-glazing was used in the manufacture of domestic pottery. Now, except for use by some studio potters, the process is obsolete. The last large-scale application before its demise in the face of environmental clean air restrictions was in the production of salt-glazed sewer-pipes.
- Ash glazing - ash from the combustion of plant matter has been used as the flux component of glazes. The source of the ash was generally the combustion waste from the fuelling of kilns although the potential of ash derived from arable crop wastes has been investigated. Ash glazes are of historical interest in the Far East although there are reports of small-scale use in other locations such as the Catawba Valley Pottery in the United States. They are now limited to small numbers of studio potters who value the unpredictability arising from the variable nature of the raw material.
Firing

Firing produces irreversible changes in the body. It is only after firing that the article or material is pottery. In lower-fired pottery, the changes include sintering, the fusing together of coarser particles in the body at their points of contact with each other. In the case of porcelain, where different materials and higher firing-temperatures are used, the physical, chemical and mineralogical properties of the constituents in the body are greatly altered. In all cases, the object of firing is to permanently harden the wares and the firing regime must be appropriate to the materials used to make them. As a rough guide, earthenwares are normally fired at temperatures in the range of about 1,000°C (1,830 °F) to 1,200 °C (2,190 °F); stonewares at between about 1,100 °C (2,010 °F) to 1,300 °C (2,370 °F); and porcelains at between about 1,200 °C (2,190 °F) to 1,400 °C (2,550 °F).
Firing pottery can be done using a variety of methods, with a kiln being the usual firing method. Both the maximum temperature and the duration of firing influences the final characteristics of the ceramic. Thus, the maximum temperature within a kiln is often held constant for a period of time to soak the wares to produce the maturity required in the body of the wares.
The atmosphere within a kiln during firing can affect the appearance of the finished wares. An oxidising atmosphere, produced by allowing air to enter the kiln, can cause the oxidation of clays and glazes. A reducing atmosphere, produced by limiting the flow of air into the kiln, can strip oxygen from the surface of clays and glazes. This can affect the appearance of the wares being fired and, for example, some glazes containing iron fire brown in an oxidising atmosphere, but green in a reducing atmosphere. The atmosphere within a kiln can be adjusted to produce complex effects in glaze.
Kilns may be heated by burning wood, coal and gas or by electricity. When used as fuels, coal and wood can introduce smoke, soot and ash into the kiln which can affect the appearance of unprotected wares. For this reason, wares fired in wood- or coal-fired kilns are often placed in the kiln in saggars, lidded ceramic boxes, to protect them. Modern kilns powered by gas or electricity are cleaner and more easily controlled than older wood- or coal-fired kilns and often allow shorter firing times to be used. In a Western adaptation of traditional Japanese Raku ware firing, wares are removed from the kiln while hot and smothered in ashes, paper or woodchips which produces a distinctive carbonised appearance. This technique is also used in Malaysia in creating traditional labu sayung.
In Mali, a firing mound is used rather than a brick or stone kiln. Unfired pots are first brought to the place where a mound will be built, customarily by the women and girls of the village. The mound's foundation is made by placing sticks on the ground, then:
[...]pots are positioned on and amid the branches and then grass is piled high to complete the mound. Although the mound contains the pots of many women, who are related through their husbands' extended families, each women is responsible for her own or her immediate family's pots within the mound. When a mound is completed and the ground around has been swept clean of residual combustible material, a senior potter lights the fire. A handful of grass is lit and the woman runs around the circumference of the mound touching the burning torch to the dried grass. Some mounds are still being constructed as others are already burning.
History
A great part of the history of pottery is prehistoric, part of past pre-literate cultures. Therefore, much of this history can only be found among the artefacts of archaeology. Because pottery is so durable, pottery and sherds from pottery survive from millennia at archaeological sites.
Before pottery becomes part of a culture, several conditions must generally be met.
- First, there must be usable clay available. Archaeological sites where the earliest pottery was found were near deposits of readily available clay that could be properly shaped and fired. China has large deposits of a variety of clays, which gave them an advantage in early development of fine pottery. Many countries have large deposits of a variety of clays.
- Second, it must be possible to heat the pottery to temperatures that will achieve the transformation from raw clay to ceramic. Methods to reliably create fires hot enough to fire pottery did not develop until late in the development of cultures.
- Third, the potter must have time available to prepare, shape and fire the clay into pottery. Even after control of fire was achieved, humans did not seem to develop pottery until a sedentary life was achieved. It has been hypothesized that pottery was developed only after humans established agriculture, which led to permanent settlements.
- Fourth, there must be a sufficient need for pottery in order to justify the resources required for its production.
Early pottery
Methods of forming: Hand-shaping was the earliest method used to form vessels. This included the combination of pinching and coiling.
Firing: The earliest method for firing pottery wares was the use of bonfires Pit fired pottery. Firing times were short but the peak-temperatures achieved in the fire could be high, perhaps in the region of 900 °C (1,650 °F), and were reached very quickly.
Clay: Early potters used whatever clay was available to them in their geographic vicinity. However, the lowest quality common red clay was adequate for low-temperature fires used for the earliest pots. Clays tempered with sand, grit, crushed shell or crushed pottery were often used to make bonfire-fired ceramics because they provided an open-body texture that allowed water. The coarser particles in the clay also acted to restrain shrinkage during drying, and hence reduce the risk of cracking.
Form: In the main, early bonfire-fired wares were made with rounded bottoms to avoid sharp angles that might be susceptible to cracking.
Glazing: the earliest pots were not glazed.
The potter's wheel was invented in Mesopotamia sometime between 6,000 and 4,000 BCE ( Ubaid period) and revolutionised pottery production.
Biscuit moulds were used to a limited extent as early as the 5th and 6th century BCE by the Etruscans and more extensively by the Romans.
Slipcasting, a popular method for shaping irregular shaped articles. It was first practised, to a limited extent, in China as early as the T'ang dynasty
Transition to kilns: The earliest intentionally constructed were pit-kilns or trench-kilns—holes dug in the ground and covered with fuel. Holes in the ground provided insulation and resulted in better control over firing.
kilns: Pit fire methods were adequate for creating earthenware, but higher-fired stoneware and porcelain required more sophisticated methods of firing using high-fire kilns (see below kilns).
History of pottery types
Earthenware
The earliest forms of pottery were made from clays that were fired at low temperatures in pit-fires or in open bonfires. They were hand formed and undecorated. Because the biscuit form of earthenware is porous, it has limited utility for storage of liquids. However, earthenware has a continuous history from the Neolithic period to today. It can be made from a wide variety of clays. The development of ceramic glaze which makes it impermeable makes it a popular and practical form of pottery making. The addition of decoration has evolved throughout its history.
Stoneware
Glazed Stoneware was being created as early as the 15th century BCE in China. This achievement coincided with kilns that could be fired at higher temperatures.
Porcelain
Porcelain was first made in China during the Tang Dynasty (618-906 CE). Porcelain was also made in Korea and Japan around the 16th and 17th century AD after suitable kaolin was located in those countries. It was not created outside of the area until the 18th century.
History by region
The earliest-known ceramic objects are Gravettian figurines such as those discovered at Dolní Věstonice in the modern-day Czech Republic. The Venus of Dolní Věstonice (Věstonická Venuše in Czech) is a Venus figurine, a statuette of a nude female figure dated to 29,000–25,000 BCE (Gravettian industry). The earliest pottery vessels date back to 20,000 BP and were discovered in Xianrendong cave in Jiangxi, China. The pottery may have been used as cookware. Other early pottery vessels include those excavated from the Yuchanyan Cave in southern China, dated from 16,000 BCE, and those found in the Amur River basin in the Russian Far East, dated from 14,000 BCE.
Other early pottery vessels include those made by the Incipient Jōmon people of Japan from around 10,500 BCE have also been found. The term " Jōmon" means "cord-marked" in Japanese. This refers to the markings made on the vessels and figures using sticks with cords during their production.
It appears that pottery was independently developed in Sub-Saharan Africa during the 11,000-10,000 BCE and in South America during the 10,000 BCE
Far East Asia
Sherds have been found in China and Japan from a period between 12,000 and perhaps as long as 18,000 years ago. As of 2012, the earliest pottery found anywhere in the world, dating to 20,000 to 19,000 years before the present, was found at Xianrendong Cave in the Jiangxi province of China. In Japan, the Jōmon period has a long history of development of Jōmon Pottery which was characterized by impressions of rope on the surface of the pottery created by pressing rope into the clay before firing. Glazed Stoneware was being created as early as the 15th century BCE in China. Porcelain became a renowned Chinese export during the Tang Dynasty (618-906 CE) and subsequent dynasties. Korean potters produced porcelain as early as the 14th century CE. Koreans brought the art of porcelain to Japan in the 17th century CE.
The secret of making such porcelain was sought in the Islamic world and later in Europe when examples were imported from the East. Many attempts were made to imitate it in Italy and France. However it was not produced outside of the Orient until 1709 in Germany.
South Asia
Pottery was in use in ancient India, including areas now forming Pakistan and northwest India, during the Mehrgarh Period II (5,500-4,800 BCE) and Merhgarh Period III (4,800-3,500 BCE), known as the ceramic Neolithic and chalcolithic. Pottery, including items known as the ed-Dur vessels, originated in regions of the Indus Valley and have been found in a number of sites in the Indus Valley Civilization.
Near East
The earliest history of pottery production in the Near East can be divided into four periods, namely: the Hassuna period (7000-6500 BCE), the Halaf period (6500-5500 BCE), the Ubaid period (5500-4000 BCE), and the Uruk period (4000-3100 BCE).
The invention of the potter's wheel in Mesopotamia sometime between 6,000 and 4,000 BCE ( Ubaid period) revolutionized pottery production. Specialized potters were then able to meet the expanding needs of the world's first cities.
Pottery making began in the Fertile Crescent from the 7th millennium BCE. The earliest forms, which were found at the Hassuna site, were hand formed from slabs, undecorated, unglazed low-fired pots made from reddish-brown clays. Within the next millennium, wares were decorated with elaborate painted designs and natural forms, incising and burnished.
By 4000 BCE, the potters wheel was developed. Newer kiln designs could fire wares to 1,050 °C (1,920 °F) to 1,200 °C (2,190 °F) which enabled new possibilities and new preparation of clays. Production was now carried out by small groups of potters for small cities, rather than individuals making wares for a family. The shapes and range of uses for ceramics and pottery expanded beyond simple vessels to store and carry to specialized cooking utensils, pot stands and rat traps.
As the region developed new organizations and political forms, pottery became more elaborate and varied. Some wares were made using moulds, allowing for increased production for the needs of the growing populations. Glazing was commonly used and pottery was more decorated.
Aegean region
Civilization developed concurrently with the Fertile Crescent in the ancient Mediterranean islands around Greece from about 3200 to 1000 BCE and carried to Ancient Greece and Ancient Rome that is considered the Classical era in the Western world. The arts of these cultures eventually became a hallmark for Europe and the New World.
The Minoan pottery was characterized by elaborate painted decoration with natural themes.
The classical Greek culture began to emerge around 1000 BCE featuring a variety of well crafted pottery which now included the human form as a decorating motif. The pottery wheel was now in regular use. Although glazing was known to these potters, it was not widely used. Instead, a more porous clay slip was used for decoration. A wide range of shapes for different uses developed early and remained essentially unchanged during the Greek history.
In the Mediterranean, during the Greek Dark Ages (1,100–800 BCE), amphoras and other pottery were decorated with geometric designs such as squares, circles and lines. In the Chalcolithic period in Mesopotamia, Halafian pottery achieved a level of technical competence and sophistication, not seen until the later developments of Greek pottery with Corinthian and Attic ware.
The Etruscan pottery carried on the Greek pottery with its own variations.
The Ancient Roman pottery started by copying Greek and Etruscan styles but soon developed a style of its own.
The distinctive Red Samian ware of the Early Roman Empire was copied by regional potters throughout the Empire.
Islamic pottery
Early Islamic pottery followed the forms of the regions which the Muslims conquered. Eventually, however, there was cross-fertilization between the regions. This was most notable in the Chinese influences on Islamic pottery. Trade between China and Islam took place via the system of trading posts over the lengthy Silk Road. Islamic nations imported stoneware and later porcelain from China. China imported the minerals for Cobalt blue from the Islamic ruled Persia to decorate their blue and white porcelain, which they then exported to the Islamic world.
Likewise, Islamic art contributed to a lasting pottery form identified as Hispano-Moresque in Andalucia (Islamic Spain). Unique Islamic forms were also developed, including fritware, lusterware and specialized glazes like tin-glazing, which led to the development of the popular maiolica.
One major emphasis in ceramic development in the Muslim world was the use of tile and decorative tilework.
Europe
The early inhabitants of Europe developed pottery at about the same time as in the Near East, circa 5500–4500 BCE. These cultures and their pottery were eventually shaped by new cultural influences and technology with the invasions of Ancient Rome and later by Islam. The Renaissance art of Europe was a melding of the art of Classical era and Islamic art.
Americas
Most evidence points to an independent development of pottery in the Amerindian cultures, starting with their Archaic Era (3500–2000 BCE), and into their Formative period (2000 BCE-200 CE). These cultures did not develop the stoneware, porcelain or glazes found in the old world.
Africa
Northern Africa includes Egypt, which had several distinct phases of development in pottery. During the early Mediterranean civilizations of the fertile crescent, Egypt developed a unique non-clay-based high-fired ceramic which has come to be called Egyptian faience.
The other major phase came during the Umayyad Caliphate of Islam, Egypt was a link between early centre of Islam in the Near East and Iberia which led to the impressive style of pottery.
As for Sub-Saharan Africa, in 2007, Swiss archeologists discovered pieces of the oldest pottery in Africa in Central Mali, dating back to at least 9,500 BCE.
Oceania
Polynesia, Melanesia, and Micronesia
Pottery has been found in archaeological sites across the islands of Oceania. It is attributed to an ancient archaeological culture called the Lapita. A form of pottery called Plainware is found throughout sites of Oceania. The relationship between Lapita pottery and Plainware is not altogether clear.
The Indigenous Australians were hunter-gatherer tribes and did not farm or cultivate crops, and in keeping with these cultural features, they also never developed pottery. After Europeans came to Australia and settled, they found deposits of clay which were analysed by English potters as excellent for making pottery. Less than 20 years later, Europeans came to Australia and began creating pottery. Since then, ceramic manufacturing, mass-produced pottery, and studio pottery have flourished in Australia.
Archaeology
For archaeologists, anthropologists and historians the study of pottery can help to provide an insight into past cultures. Pottery is durable, and fragments, at least, often survive long after artefacts made from less-durable materials have decayed past recognition. Combined with other evidence, the study of pottery artefacts is helpful in the development of theories on the organisation, economic condition and the cultural development of the societies that produced or acquired pottery. The study of pottery may also allow inferences to be drawn about a culture's daily life, religion, social relationships, attitudes towards neighbours, attitudes to their own world and even the way the culture understood the universe.
Chronologies based on pottery are often essential for dating non-literate cultures and are often of help in the dating of historic cultures as well. Trace-element analysis, mostly by neutron activation, allows the sources of clay to be accurately identified and the thermoluminescence test can be used to provide an estimate of the date of last firing. Examining fired pottery shards from prehistory, scientists learned that during high-temperature firing, iron materials in clay record the exact state of Earth's magnetic field at that exact moment.
Environmental issues in production
Although many of the environmental effects of pottery production have existed for millennia, some of these have been amplified with modern technology and scales of production. The principal factors for consideration fall into two categories: (a) effects on workers, and (b) effects on the general environment. Within the effects on workers, chief impacts are indoor air quality, sound levels and possible over-illumination. Regarding the general environment, factors of interest are fuel consumption, off-site water pollution, air pollution and disposal of hazardous materials.
Historically, "plumbism" ( lead poisoning) was a significant health concern to those glazing pottery. This was recognised at least as early as the nineteenth century, and the first legislation in the United Kingdom to limit pottery workers’ exposure was introduced in 1899. While the risk to those working in ceramics is now much reduced, it can still not be ignored. With respect to indoor air quality, workers can be exposed to fine particulate matter, carbon monoxide and certain heavy metals. The greatest health risk is the potential to develop silicosis from the long-term exposure to crystalline silica. Proper ventilation can reduce the risks, and the first legislation in the United Kingdom to govern ventilation was introduced in 1899. Another, more recent, study at Laney College, Oakland, California suggests that all these factors can be controlled in a well-designed workshop environment.
The use of energy and pollutants in the production of ceramics is a growing concern. Electric firing is arguably more environmentally friendly than combustion firing although the source of the electricity varies in environmental impact.
Other usages
The English city of Stoke-on-Trent is widely known as The Potteries because of the large number of pottery factories or, colloquially, Pot Banks. It was one of the first industrial cities of the modern era where, as early as 1785, two hundred pottery manufacturers employed 20,000 workers. For the same reason, the largest football club in the city is known as The Potters.