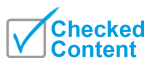
Kevlar
Background to the schools Wikipedia
SOS Children offer a complete download of this selection for schools for use on schools intranets. SOS Children works in 45 African countries; can you help a child in Africa?
Kevlar is the registered trademark for a light, strong para-aramid synthetic fibre, related to other aramids such as Nomex and Technora.
Developed at DuPont in 1965 by Stephanie Kwolek and Roberto Berendt, it was first commercially used in the early 1970s. Typically it is spun into ropes or fabric sheets that can be used as such or as an ingredient in composite material components.
Currently, Kevlar has many applications, ranging from bicycle tires and racing sails to body armor because of its high strength-to-weight ratio—famously: "...5 times stronger than steel on an equal weight basis...".
A similar fibre called Twaron with roughly the same chemical structure was introduced by Akzo in 1978, and now manufactured by Teijin.
Properties
When Kevlar is spun, the resulting fibre has great tensile strength (ca. 3 000 MPa), a relative density of 1.44, and does not rust. When used as a woven material, it is suitable for mooring lines and other underwater application objects.
There are three grades of Kevlar: (i) Kevlar, (ii) Kevlar 29, and (iii) Kevlar 49. Typically, Kevlar is used as reinforcement in tires and rubber mechanical goods. Kevlar 29's industrial applications are as cables, in asbestos replacement, brake linings, and body armour. Kevlar 49 has the greatest tensile strength of all the aramids, and is used in plastic reinforcement for boat hulls, airplanes, and bicycles. The ultraviolet light component of sunlight degrades and decomposes Kevlar, hence it is rarely used outdoors without protection against sunlight.
Although Kevlar has excellent properties to tensile strength, there must be studied the low friction coefficient. It would compromise the structural integrity of the material. An application of Kevlar (49 or 149) like resistant material to friction, are discs of clutches systems.
Aha Whyy Did It Delete Our Wonderful Messages, I Think Its Cus Its Gay...=D
Production
Kevlar is synthesised from the monomers 1,4- phenylene-diamine ( para-phenylenediamine) and terephthaloyl chloride in condensation reaction yielding hydrochloric acid as a byproduct. The result is a liquid-crystalline behaviour and mechanical drawing orienting the polymer chains in the fibre's direction. Hexamethylphosphoramide (HMPA) was the polymerization solvent first used, but toxicology tests demonstrated it provoked tumors in the noses of rats, so DuPont replaced it by a N-methyl-pyrrolidone and calcium chloride as the solvent. As this process was patented by Akzo (see above) in the production of Twaron, a patent war ensued.
Kevlar (poly paraphenylene terephthalamide) production is expensive because of the difficulties arising from using corrosive concentrated sulfuric acid, needed to keep the water-insoluble polymer in solution during its synthesis and spinning.
Chemical properties
Fibers of Kevlar consist of long molecular chains produced from PPTA (poly-paraphenylene terephthalamide). There are many inter-chain bonds making the material extremely strong. Kevlar derives part of its high strength from inter-molecular hydrogen bonds formed between the carbonyl groups and protons on neighboring polymer chains and the partial pi stacking of the benzenoid aromatic stacking interactions between stacked strands. These interactions have a greater influence on Kevlar than the van der Waals interactions and chain length that typically influence the properties of other synthetic polymers and fibers such as Dyneema. The presence of salts and certain other impurities, especially calcium, could interfere with the strand interactions and caution is used to avoid inclusion in its production. Kevlar's structure consists of relatively rigid molecules which tend to form mostly planar sheet-like structures rather like silk protein.
Thermal properties
For a polymer Kevlar has very good resistance to high temperatures, and maintains its strength and resilience down to cryogenic temperatures (-196°C); indeed, it is slightly stronger at low temperatures.
At higher temperatures the tensile strength is immediately reduced by about 10-20%, and after some hours the strength progressively reduces further. For example at 160°C about 10% reduction in strength occurs after 500 hours. At 260°C 50% reduction occurs after 70 hours.
At 450°C Kevlar sublimates.
Applications
Armour
Kevlar is well-known as a component of some bulletproof vests. The PASGT helmet and vest used by US military forces since the early 1980s both have Kevlar as a key component, as do their replacements. Civilian applications include Kevlar reinforced clothing for motorcycle riders to protect against abrasion injuries and also Emergency Service's protection gear if it involves high heat (e.g., tackling a fire).
Sports equipment
In many cases it is part of a composite material, used in the production of some tennis, badminton and squash rackets, kayaks, and some field hockey and lacrosse sticks. It is used as an inner lining for some bicycle tires to prevent punctures, and due to its excellent heat resistance, is used for fire poi wicks. It is used for Motorcycle safety clothing, especially in the areas featuring padding such as shoulders and elbows. It was also used as speed control patches for certain soap shoes models.
Audio equipment
It has also been found to have useful acoustic properties for loudspeaker cones, specifically for bass and midrange drive units.
Electricity generation
It was used by scientists from Georgia Tech as a base textile for an experiment in electricity-producing clothing. This was done by weaving zinc-oxide nanowires into the fabric. If successful, the new fabric would generate about 80 miliwatts per square meter.