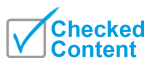
Lockheed Martin F-35 Lightning II
Background to the schools Wikipedia
SOS Children offer a complete download of this selection for schools for use on schools intranets. To compare sponsorship charities this is the best sponsorship link.
F-35 Lightning II | |
---|---|
An F-35C Lightning II, marked CF-1, conducts a test flight over the Chesapeake Bay in February 2011 | |
Role | Stealth multirole fighter |
National origin | United States |
Manufacturer | Lockheed Martin Aeronautics |
First flight | 15 December 2006 |
Introduction | After 2016 |
Status | In initial production and testing, used for training by U.S. |
Primary users | United States Air Force United States Marine Corps United States Navy Royal Air Force |
Produced | 2006–present |
Number built | 63 |
Unit cost | F-35A: US$107 million (sans engine, 5th LRIP) F-35B: US$237.7M (weap. sys. cost, 2012) F-35C: US$236.8M (weap. sys. cost, 2012) |
Developed from | Lockheed Martin X-35 |
The Lockheed Martin F-35 Lightning II is a family of single-seat, single-engine, fifth generation multirole fighters under development to perform ground attack, reconnaissance, and air defense missions with stealth capability. The F-35 has three main models; the F-35A is a conventional takeoff and landing variant, the F-35B is a short take-off and vertical-landing variant, and the F-35C is a carrier-based variant.
The F-35 is descended from the X-35, the product of the Joint Strike Fighter (JSF) program. JSF development is being principally funded by the United States. The partner nations are either NATO members or close U.S. allies. It is being designed and built by an aerospace industry team led by Lockheed Martin. The F-35 carried out its first flight on 15 December 2006.
The United States plans to buy a total of 2,443 aircraft to provide the bulk of its tactical airpower for the U.S. Air Force, Marine Corps and Navy over the coming decades. The United Kingdom, Italy, Netherlands, Australia, Canada, Norway, Denmark, and Turkey are part of the development program; Israel, Singapore and Japan may also equip their air services with the F-35.
Development
JSF Program requirements and selection
The JSF program was designed to replace the United States military F-16, A-10, F/A-18 (excluding newer E/F "Super Hornet" variants) and AV-8B tactical fighter aircraft. To keep development, production, and operating costs down, a common design was planned in three variants that share 80 percent of their parts:
- F-35A, conventional take off and landing ( CTOL) variant.
- F-35B, short-take off and vertical-landing ( STOVL) variant.
- F-35C, carrier-based CATOBAR (CV) variant.
George Standridge of Lockheed Martin predicted in 2006 that the F-35 will be four times more effective than legacy fighters in air-to-air combat, eight times more effective in air-to-ground combat, and three times more effective in reconnaissance and suppression of air defenses – while having better range and requiring less logistics support and having around the same procurement costs (if development costs are ignored) as legacy fighters. The design goals call for the F-35 to be the premier strike aircraft through 2040 and be second only to the F-22 Raptor in air superiority.
The JSF development contract was signed on 16 November 1996, and the contract for System Development and Demonstration (SDD) was awarded on 26 October 2001 to Lockheed Martin, whose X-35 beat the Boeing X-32. Although both aircraft met or exceeded requirements, the X-35 design was considered to have less risk and more growth potential. The designation of the new fighter as "F-35" is out-of-sequence with standard DoD aircraft numbering, by which it should have been "F-24". It came as a surprise even to Lockheed, which had been referring to the aircraft in-house by this expected designation.
The development of the F-35 is unusual for a fighter aircraft in that no two-seat trainer versions have been built for any of the variants; advanced flight simulators mean that no trainer versions were deemed necessary. Instead F-16s have been used as bridge trainers between the T-38 and the F-35. The T-X was intended to be used to train future F-35 pilots, but this might succumb to budget pressures in the USAF.
Design phase
Based on wind tunnel testing, Lockheed Martin slightly enlarged its X-35 design into the F-35. The forward fuselage is 5 inches (130 mm) longer to make room for avionics. Correspondingly, the horizontal stabilators were moved 2 inches (51 mm) rearward to retain balance and control. The top surface of the fuselage was raised by 1 inch (25 mm) along the centre line. Also, it was decided to increase the size of the F-35B STOVL variant's weapons bay to be common with the other two variants. Manufacturing of parts for the first F-35 prototype airframe began in November 2003.
The F-35B STOVL variant was in danger of missing performance requirements in 2004 because it weighed too much; reportedly, by 2,200 lb (1,000 kg) or 8 percent. In response, Lockheed Martin added engine thrust and thinned airframe members; reduced the size of the common weapons bay and vertical stabilizers; re-routed some thrust from the roll-post outlets to the main nozzle; and redesigned the wing-mate joint, portions of the electrical system, and the portion of the aircraft immediately behind the cockpit. Many of the changes were applied to all three variants to maintain high levels of commonality. By September 2004, the weight reduction effort had reduced the aircraft's design weight by 2,700 pounds (1,200 kg). but the redesign cost $6.2 billion and delayed the project by 18 months.
On 7 July 2006, the U.S. Air Force officially announced the name of the F-35: Lightning II, in honour of Lockheed's World War II-era twin-prop Lockheed P-38 Lightning and the Cold War-era jet, the English Electric Lightning. English Electric Company's aircraft division was a predecessor of F-35 partner BAE Systems. Lightning II was also an early company name for the fighter that was later named the F-22 Raptor.
On 19 December 2008, Lockheed Martin rolled out the first weight-optimized F-35A (designated AF-1). It was the first F-35 to be produced at a full production speed and is structurally identical to the production F-35As that were delivered starting in 2010.
Lockheed Martin Aeronautics is the prime contractor and performs aircraft final assembly, overall system integration, mission system, and provides forward fuselage, wings and flight controls system. Northrop Grumman provides Active Electronically Scanned Array (AESA) radar, electro-optical Distributed Aperture System (DAS), Communications, Navigation, Identification (CNI), centre fuselage, weapons bay, and arrestor gear. BAE Systems provides aft fuselage and empennages, horizontal and vertical tails, crew life support and escape systems, Electronic warfare systems, fuel system, and Flight Control Software (FCS1). Alenia will perform final assembly for Italy and, according to an Alenia executive, assembly of all European aircraft with the exception of Turkey and the United Kingdom. The F-35 program has seen a great deal of investment in automated production facilities. For example, Handling Specialty produced the wing assembly platforms for Lockheed Martin. In November 2009, Jon Schreiber, head of F-35 international affairs program for the Pentagon, said that the U.S. will not share the software code for the F-35 with its allies.
On 5 January 2009, six F-35s had been built, including AF-1 and AG-1; another 13 pre-production test aircraft and four production aircraft were being manufactured. On 6 April 2009, U.S. Secretary of Defense Robert Gates proposed speeding up production for the U.S. to buy 2,443 F-35s.
In August 2010, Lockheed Martin announced delays in resolving a "wing-at-mate overlap" production problem, which would slow initial production.
Program cost increases and further delays
In 2006, the GAO warned that excessive concurrency between the production of additional F-35 aircraft and testing of their design might result in expensive refits for several hundred aircraft planned to be produced before completion of tests. In November 2010, the GAO found that "Managing an extensive, still-maturing global network of suppliers adds another layer of complexity to producing aircraft efficiently and on-time" and that "due to the extensive amount of testing still to be completed, the program could be required to make alterations to its production processes, changes to its supplier base, and costly retrofits to produced and fielded aircraft, if problems are discovered." USAF budget data in 2010, along with other sources, projected the F-35 to have a flyaway cost from US$89 million to US$200 million over the planned production run. In February 2011, the Pentagon put a price of $207.6 million on each of the 32 aircraft to be acquired in FY2012, rising to $304.15 million ($9,732.8/32) if its share of RDT&E spending is included.
In 2011, program head Vice Adm. David Venlet confirmed that the concurrency built into the program "was a miscalculation". This was during a contract dispute where the Pentagon insisted that Lockheed Martin help cover the costs of applying fixes found during testing to aircraft already produced. Lockheed Martin objected that the cost sharing posed an uninsurable unbounded risk that the company could not cover, and later responded that the "concurrency costs for F-35 continue to reduce". The Senate Armed Services Committee strongly backed the Pentagon position. In December 2011, Lockheed Martin agreed to a cost sharing agreement. The Aerospace Industries Association trade group warned that such changes would force them to anticipate cost overruns in their future contract bids. As of 2012, problems found in flight testing were expected to continue to lead to elevated levels of engineering changes (to be made to newly produced aircraft and retrofitted onto previously produced aircraft) through 2019. The total additional cost for concurrency in the program is around $1.3 billion. By the next year the cost had grown to $1.7 billion.
In 2012, General Norton A. Schwartz decried the "foolishness" of reliance on computer models to settle the final design of the aircraft before flight testing found the issues that needed redesign. In 2013, JSF project team leader USAF Lieutenant General Chris Bogdan said that "A large amount of concurrency, that is, beginning production long before your design is stable and long before you've found problems in test, creates downstream issues where now you have to go back and retrofit airplanes and make sure the production line has those fixes in them. And that drives complexity and cost". Bogdan did however praise the "magical" improvement in the program ever since Lockheed was forced to assume some of the financial risks.
On 21 April 2009, media reports, citing Pentagon sources, said that during 2007 and 2008, computer spies had managed to copy and siphon off several terabytes of data related to the F-35's design and electronics systems, potentially enabling the development of defense systems against the aircraft. Lockheed Martin has rejected suggestions that the project has been compromised, saying that it "does not believe any classified information had been stolen". Other sources have suggested that the incident caused a redesign of the aircraft's hardware and software to be more resistant to cyber attack. BAE Systems was reported to be the target of the cyber espionage that may have stolen secrets related to the F-35. An additional problem emerged when it was feared that China had intercepted telemetry from F-35 test flights. In 2013 a report from Mandiant tracked the hacking to a unit of the People's Liberation Army.
On 9 November 2009, Ashton Carter, under-secretary of defense for acquisition, technology and logistics, acknowledged that the Pentagon "joint estimate team" (JET) had found possible future cost and schedule overruns in the project and that he would be holding meetings to attempt to avoid these. On 1 February 2010, Gates removed the JSF Program Manager, U.S. Marine Corps Major General David Heinz, and withheld $614 million in payments to Lockheed Martin because of program costs and delays.
On 11 March 2010, a report from the Government Accountability Office to United States Senate Committee on Armed Services projected the overall unit cost of an F-35A to be $112M in today's money. In 2010, Pentagon officials disclosed that the F-35 program has exceeded its original cost estimates by more than 50 percent. An internal Pentagon report critical of the JSF project states that "affordability is no longer embraced as a core pillar". On 24 March, Gates termed the cost overruns and delays as "unacceptable" in a testimony before the U.S. Congress. He characterized previous cost and schedule estimates for the project as "overly rosy". Gates insisted the F-35 would become "the backbone of U.S. air combat for the next generation" and informed the Congress that he had expanded the development period by an additional 13 months and budgeted $3 billion more for the testing program while slowing down production. Lockheed Martin expects to reduce government cost estimates by 20%.
In November 2010, as part of a cost-cutting measure, the co-chairs of the National Commission on Fiscal Responsibility and Reform suggested canceling procurement of the F-35B and halving orders of F-35As and F-35Cs. At the same time, Air Force Magazine reported that "Pentagon officials" were considering canceling the F-35B because its short range means that the bases or ships it operates from will be within range of hostile tactical ballistic missiles. Lockheed Martin consultant Loren B. Thompson said that this rumor was merely a result of the usual tensions between the U.S. Navy and Marine Corps, and there was no alternative to the F-35B as an AV-8B replacement. He also confirmed that there would be further delays and cost increases in the development process because of technical problems with the aircraft and software, and blamed most of the delays and extra costs on redundant flight tests.
The Centre for Defense Information estimated that the program would be restructured with an additional year of delay and $5 billion in additional costs. On 5 November 2010, the Block 1 software flew for the first time on BF-4 which included information fusion and initial weapons-release capability. As of the end of 2010, only 15% of the software remained to be written, but this included the most difficult sections such as data fusion. In 2011, it was revealed that only 50% of the eight million lines of code had been written and that it would take another six years and 110 additional software engineers in order to complete the software for this new schedule. The total estimated lines of code for the entire program (onboard and offboard) had grown from 15 million lines to 24 million lines by 2012.
In January 2011, Defense Secretary Robert Gates expressed the Pentagon's frustration with the rising costs of the F-35 program when he said "The culture of endless money that has taken hold must be replaced by a culture of restraint." Focusing his attention on the troubled F-35B, Gates ordered "a two-year probation", saying it "should be canceled" if corrections are unsuccessful. Gates has stated his support for the program. Some private analysts, such as Richard Aboulafia, of the Teal Group state that the F-35 program is becoming a money pit. Gates' successor, Leon Panetta, ended the F-35B's probation on 20 January 2012, stating "The STOVL variant has made — I believe and all of us believe — sufficient progress."
Former Pentagon manager Paul G. Kaminski has said that the lack of a complete test plan has added five years to the JSF program. As of February 2011, the main flaws with the aircraft were engine "screech", transonic wing roll-off and display flaws in the helmet-mounted display.
The current schedule has the delivery of basic combat capability aircraft in late 2015, followed by full capability block three software in late 2016. The $56.4 billion development project for the aircraft should be completed in 2018 when the block five configuration is expected to be delivered, several years late and considerably over budget.
Delays in the F-35 program may lead to a "fighter gap" where America and other countries will lack sufficient jet fighters to cover their requirements. Israel may seek to buy second-hand F-15s to cover its gap, while Australia may also seek to buy more Super Hornets from the USN to cover their own capability gap in the face of F-35 delays.
Initial Operational Capability (IOC) will be determined by software development rather than by hardware production or pilot training.
In May 2011, the Pentagon's top weapons buyer Ashton Carter said that its new $133 million unit price was not affordable.
In 2011, The Economist warned that the F-35 was in danger of slipping into a "death spiral" where increasing per-aircraft costs would lead to cuts in number of aircraft ordered which would lead to further cost increases and further order cuts. Later that year, four aircraft were cut from the fifth LRIP order to pay for cost overruns. And, in 2012, a further two aircraft were cut. Lockheed acknowledged that the slowing of purchases would increase the costs. David Van Buren, acquisition chief for the U.S. Air Force, said that Lockheed would need to cut infrastructure to match the reduced market for their aircraft. The company said that the slowdown in American orders will free up capacity to meet the urgent short term needs of foreign partners for replacement fighters. But Air Force Secretary Michael Donley said that there was no more money available for the project and that future price increases would be matched with cuts in the number of aircraft ordered. Later that month, the Pentagon reported that costs had risen another 4.3 percent, partially as a result of production delays. In 2012, the purchase of six out of 31 aircraft was tied to performance metrics of the program. In 2013 Bogdan repeated that no more money was available, but that he hoped to avoid the death spiral.
Japan has warned that it may halt their purchase if the unit costs increase, and Canada has indicated it has not fully committed to purchasing the aircraft. The United States is projected to spend an estimated US$323 billion for development and procurement on the F-35 program, making it the most expensive defense program ever. The total life-cycle cost for the entire American fleet is estimated to be US$1.51 trillion over its 50-year life, or $618 million per plane. Testifying before a Canadian parliamentary committee in 2011, Rear Admiral Arne Røksund of Norway estimated that his country's 52 F-35 fighter jets will cost $769 million each over their operational lifetime.
In 2011, a Congressional Joint Strike Fighter Caucus was formed by some of the top recipients of Lockheed Martin contributions.
The program delays have affected the program's worldwide supply chain, causing Australian Quickstep Holdings to struggle for capital, in spite of their 20-year contract with Lockheed Martin.
In order to reduce the estimated $1 trillion cost of the F-35 program over its 50-year lifetime, the USAF is considering reducing Lockheed's role in Contractor Logistics Support for the fighter. Lockheed has responded that the trillion dollar estimate relies on future costs beyond its control such as USAF reorganizations and upgrades to the aircraft that have yet to be specified.
In 2012, in order to avoid further redesign delays, the U.S. DoD accepted a reduced combat radius for the F-35A and a longer takeoff run for the F-35B. The F-35B's estimated radius has also decreased 15 percent from initial JSF goal. In a meeting in Sydney in March, the United States pledged to eight partner nations that there would be no more program delays.
On 31 May 2012, Lockheed Chief Executive Bob Stevens complained that the Defense Department's requirements for cost data were driving up the cost of the program. The same week he admitted that a strike over the company's plans to strip benefits from workers might cause a shortfall in the plan to produce 29 F-35s that year. The striking union workers raised questions about the standards of the replacement workers, even as their own work had been cited for "inattention to production quality" with a 16% rework rate. The workers went on strike to protect pensions whose costs have been the subject of negotiations with the Department of Defense over the costs of the next batch of aircraft. These same pension costs were cited by Fitch in their downgrade of the outlook for Lockheed Martin's stock price. Stevens said that while he hoped to bring down the costs of the program, the industrial base was not capable of meeting the government's expectations of affordability. He was able to force concessions on the workers while retaining top management's generous bonuses and pensions.
According to the latest Government Accountability Office report, the F-35's unit cost has almost doubled, an increase of 93% over the program's 2001 baseline cost estimates. Lockheed fears that if the tighter policies for award fees of the Obama administration are not reversed, their profits on the aircraft will be reduced by $500 million over the next five years. This was demonstrated in 2012 when the Pentagon withheld the maximum $47 million allowed for Lockheed's failure to certify its program to track project costs and schedules. The GAO has also faulted the USAF and USN for not fully planning out the full costs required to extend legacy F-16 and F-18 fleets to cover for delays in the F-35 program.
In 2013 Lockheed began to lay off workers at the Fort Worth plant where the F-35s were assembled. They said that the currently estimated concurrency costs of refitting the 187 aircraft that will have been built by the time testing concludes in 2016 to reflect the lessons learned during that testing are now less than previously feared. The GAO's Michael Sullivan said that when Lockheed started the program they had failed to get an early start on the systems engineering and had not understood the requirements or the technologies. The Pentagon vowed to continue funding the program during budget sequestration if possible.
Western analysts have noted that while the Chengdu J-20 and Shenyang J-31 are expected to fall far short of the capabilities of the F-35, the delays in providing the American fifth generation fighter in sufficient numbers to American allies in the region may give China a window of opportunity over the legacy fighters of their neighbors.
Concerns over performance and safety
In 2006, the F-35 was downgraded from "very low observable" to "low observable", a change former RAAF flight test engineer Peter Goon likened to increasing the radar cross section from a marble to a beach ball. A Parliamentary Inquiry asked what was the re-categorization of the terminology in the United States such that the rating was changed from "very low observable" to "low observable". The Department of Defence said that the change in categorization by the U.S. was due to a revision in procedures for discussing stealth platforms in a public document. The previous decision to re-categorize in the public domain has now been reversed. Publicly released material now categorizes JSF as very low observable (VLO).
The spark that set off the row of criticism was US Ambassador Tom Schieffer's confirmation to the Joint Standing Committee on Foreign Affairs (JSCFADT) on 21 June 2004: "With regard to the stealth technology, the airplane that Australia will get will be the stealthiest airplane that anybody outside the United States can acquire. We have given assurances to Australia that we will give you the absolute maximum that we can with regard to that technology. Having said that, the airplane will not be exactly the same airplane as the United States will have. But it will be a stealth fighter; it will have stealth capabilities; and it will be at the highest level that anyone in the world has outside the United States." The F-35's stealth would be similar to contemporary aircraft. A follow on article in Janes Defence Weekly, 26 April 2006, by Tom Burbage from Lockheed Martin states that the US will not export key technologies such as stealth. Before, a Jane's article gave a hint that US$1B, spent on several contracts, would serve to protect stealth technology and probably provide for a less stealthy export configuration of the fighter.
In response to Air Power Australia's criticisms, Australia's Air Vice Marshal Osley said that "Air Power Australia (Kopp and Goon) claim that the F35 will not be competitive in 2020 and that Air Power Australia's criticisms mainly centre around F35's aerodynamic performance and stealth capabilities." Osley continued with, "these are inconsistent with years of detailed analysis that has been undertaken by Defence, the JSF program office, Lockheed Martin, the U.S. services and the eight other partner nations. While aircraft developments such as the Russian PAK-FA or the Chinese J20, as argued by Airpower Australia, show that threats we could potentially face are becoming increasingly sophisticated, there is nothing new regarding development of these aircraft to change Defence's assessment." He then said that he thinks that the Air Power Australia's "analysis is basically flawed through incorrect assumptions and a lack of knowledge of the classified F-35 performance information."
Andrew Krepinevich has questioned the reliance on "short range" aircraft like the F-35 or F-22 to "manage" China in a future conflict and has suggested reducing the number of F-35s ordered in favour of a longer range platform like the Next-Generation Bomber, but Michael Wynne, then United States Secretary of the Air Force rejected this plan of action in 2007. By 2012, Wynne had conceded that America's short ranged fifth generation fighters would need drop tanks in order to be effective. In 2011, the Centre for Strategic and Budgetary Assessments (CSBA) pointed to the restructuring of the F-35 program and the return of the bomber project as a sign of their effectiveness, while Rebecca Grant said that the restructuring was a "vote of confidence" in the F-35 and "there is no other stealthy, survivable new fighter program out there". Lockheed has also said that the F-35 is designed to launch internally carried bombs at supersonic speed and internal missiles at maximum supersonic speed.
In 2008, it was reported that RAND Corporation conducted simulated war games in which Russian Sukhoi Su-35 fighters defeated the F-35. As a result of these media reports, then Australian defence minister Joel Fitzgibbon requested a formal briefing from the Australian Department of Defence on the simulation. This briefing stated that the reports of the simulation were inaccurate and did not actually compare the F-35's flight performance against other aircraft.
The Pentagon and Lockheed Martin added that these simulations did not address air-to-air combat. A Lockheed Martin press-release points to USAF simulations regarding the F-35's air-to-air performance against potential adversaries described as " 4th generation" fighters, in which it claims the F-35 is "400 percent" more effective. Major General Charles R. Davis, USAF, the F-35 program executive officer, has stated that the "F-35 enjoys a significant Combat Loss Exchange Ratio advantage over the current and future air-to-air threats, to include Sukhois". The nature of the simulations, and the terms upon which the "400 percent" figure have been derived remains unclear.
In March 2012, Tom Burbage, and Gary Liberson, of Lockheed Martin addressed an Australian Parliamentary Committee about earlier assessments. They stated "Time has moved on since 2008 and we know a lot more about this airplane now than we knew then. ... Our current assessment that we speak of is greater than 6 to 1 relative loss exchange ratio against, in 4 versus 8 engagement scenarios—4 blue F-35s versus 8 advanced red threats in the 2015 to 2020 time frame. And it is very important to note that is without the pilot in the loop and are the lowest number that we talk about, the greater than 6 to 1 is when we include the pilot in the loop [simulator] activities". They said: "we actually have a fifth-gen airplane flying today. The F22 has been in many exercises and is much better than the simulations forecast. We have F35 flying today; it has not been put into that scenario yet, but we have very high quality information on the capability of the sensors and the capability of the airplane, and we have represented the airplane fairly and appropriately in these large-scale campaign models that we are using. But it is not just us—it is our air force; it is your air force; it is all the other participating nations that do this; it is our navy and our marine corps that do these exercises. It is not Lockheed in a closet gleaning up some sort of result." Although the advanced threats are classified they indicated that all the first-tier air forces in the world would not look at analysis against inferior threats."
Regarding the original plan to fit the F-35 with only two air-to-air missiles (internally), Major Richard Koch, chief of USAF Air Combat Command’s advanced air dominance branch is reported to have said that "I wake up in a cold sweat at the thought of the F-35 going in with only two air-dominance weapons." The Norwegians have been briefed on a plan to equip the F-35 with six AIM-120D missiles by 2019.
Former RAND author John Stillion has written of the F-35A's air-to-air combat performance that it “can’t turn, can’t climb, can’t run”, but Lockheed Martin test pilot Jon Beesley has countered that in an air-to-air configuration the F-35 has almost as much thrust as weight and a flight control system that allows it to be fully maneuverable even at a 50-degree angle of attack.
Andrew Hoehn, Director of RAND Project Air Force, made the following statement: “Recently, articles have appeared in the Australian press with assertions regarding a war game in which analysts from the RAND Corporation were involved. Those reports are not accurate. RAND did not present any analysis at the war game relating to the performance of the F-35 Joint Strike Fighter, nor did the game attempt detailed adjudication of air-to-air combat. Neither the game nor the assessments by RAND in support of the game undertook any comparison of the fighting qualities of particular fighter aircraft.”
In an interview with the state-run Global Times, Chen Hu, editor-in-chief of World Military Affairs magazine has said that the F-35 is too costly because it attempts to provide the capabilities needed for all three American services in a common airframe. Dutch news program NOVA show interviewed U.S. defense specialist Winslow T. Wheeler and aircraft designer Pierre Sprey who called the F-35 "heavy and sluggish" as well as having a "pitifully small load for all that money", and went on to criticize the value for money of the stealth measures as well as lacking fire safety measures. His final conclusion was that any air force would be better off maintaining its fleets of F-16s and F/A-18s compared to buying into the F-35 program. Lockheed spokesman John Kent has said that the missing fire-suppression systems would have offered "very small" improvements to survivability.
In the context of selling F-35s to Israel to match the F-15s that will be sold to Saudi Arabia, a senior U.S. defense official was quoted as saying that the F-35 will be "the most stealthy, sophisticated and lethal tactical fighter in the sky," and added "Quite simply, the F-15 will be no match for the F-35." After piloting the aircraft, RAF Squadron Leader Steve Long said that, over its existing aircraft, the F-35 will give "the RAF and Navy a quantum leap in airborne capability."
Consultant to Lockheed Martin Loren B. Thompson has said that the "electronic edge F-35 enjoys over every other tactical aircraft in the world may prove to be more important in future missions than maneuverability".
In 2011, Canadian politicians raised the issue of the safety of the F-35's reliance on a single engine (as opposed to a twin-engine configuration, which provides a backup in case of an engine failure). Canada, and other operators, had previous experience with a high-accident rate with the single-engine Lockheed CF-104 Starfighter with many accidents related to engine failures. Defence Minister Peter MacKay, when asked what would happen if the F-35's single engine fails in the Far North, stated "It won’t".
In November 2011, a Pentagon study team identified the following 13 areas of concern that remained to be addressed in the F-35:
- The helmet-mounted display system does not work properly.
- The fuel dump subsystem poses a fire hazard.
- The Integrated Power Package is unreliable and difficult to service.
- The F-35C's arresting hook does not work.
- Classified "survivability issues", which have been speculated to be about stealth.
- The wing buffet is worse than previously reported.
- The airframe is unlikely to last through the required lifespan.
- The flight test program has yet to explore the most challenging areas.
- The software development is behind schedule.
- The aircraft is in danger of going overweight or, for the F-35B, not properly balanced for VTOL operations.
- There are multiple thermal management problems. The air conditioner fails to keep the pilot and controls cool enough, the roll posts on the F-35B overheat, and using the afterburner damages the aircraft.
- The automated logistics information system is partially developed.
- The lightning protection on the F-35 is uncertified, with areas of concern.
In December 2011 the Pentagon and Lockheed came to an agreement to assure funding and delivery for a fifth order of early F-35 aircraft of yet undefined type in spite of general national austerity measures affecting the program.
Michael Auslin of the American Enterprise Institute has questioned the capability of the F-35 to engage modern air defenses, in spite of Russia's own admission that the S-300 systems are vulnerable to the F-35. In July 2012, the Pentagon awarded Lockheed another $450 million to improve the F-35 electronic warfare systems and incorporate Israeli systems.
A report released in 2013 stated that flaws in the Lightning II's fuel tank and fueldraulic systems have left it even more vulnerable to lightning strikes and other fire sources including enemy fire than previously revealed, especially when operating at lower altitudes. The same report also noted performance degradation of the three variants. The sustained turn rates of the three variants was reduced to 4.6 g for the F-35A, 4.5 g for the F-35B, and 5.0 g for the F-35C. The acceleration performance of all three variants was also downgraded, with the F-35C taking 43 seconds longer than an F-16 to accelerate from Mach 0.8 to Mach 1.2. This was judged by several fighter pilots to be a lower performance level than expected from a fourth generation fighter. The F-35 program office is reconsidering adding the removed safety equipment back in.
On 22 February 2013, the U.S. fleet of F-35s was grounded after a routine inspection of a F-35A at Edwards Air Force Base found a crack in an engine turbine blade.
USAF test pilots have noted a lack of visibility from the F-35 cockpit during evaluation flights and said that this will get them shot down in every combat. Defense spending analyst Winslow Wheeler concluded from the flight evaluation reports that the F-35A "is flawed beyond redemption", while program manager Bogdan suggested that pilots worried about being shot down should fly cargo aircraft instead. The same report found (in addition to the usual problems with the aircraft listed above):
- Current aircraft software is inadequate for even basic pilot training.
- Ejection seat may fail causing pilot fatality.
- Several pilot-vehicle interface issues, including lack of feedback on touch screen controls.
- The radar performs poorly, if at all.
- Engine replacement takes an average of 52 hours, instead of the two hours specified.
- And the maintenance tools do not work.
The JPO responded that more experienced pilots would be able to safely operate the aircraft and that procedures would improve over time. And the USAF began pilot training in March 2013.
Problems with Lockheed Martin
In September 2012, the Pentagon criticized, quite publicly, Lockheed Martin's performance on the F-35 program and stated that it would not bail out the program again if problems with the plane's systems, particularly the helmet-mounted display, were not resolved. The deputy F-35 program manager said that the government's relationship with the company was the "worst I've ever seen" in many years of working on complex acquisition programs. Air Force Secretary Michael Donley told reporters the Pentagon had no more money to pour into the program after three costly restructurings in recent years. He said the department was done with major restructuring and that there was no further flexibility or tolerance for that approach. This criticism followed a "very painful" 7 September review that focused an array of ongoing program challenges. Lockheed Martin responded with a brief statement saying it would continue to work with the F-35 program office to deliver the new fighter.
On 28 September 2012, the Pentagon announced that the F-35 Joint Strike Fighter support program would become an open competition. They invited companies to participate in a two-day forum on 14–15 November for possible opportunities to compete for work managing the supply chain of the aircraft. Their reason is to reduce F-35 life-cycle costs by creating competition within the program and to refine its acquisition strategy and evaluate alternatives that will deliver the best value, long-term F-35 sustainment solution. This could be hazardous to Lockheed, as they are the current prime contractor for sustainment of all three variants, and selection of another company could reduce their revenues.
In 2013, the officer in charge of the program blamed Lockheed and Prat for gouging the government on costs, instead of focusing on the long term future of the program.
Upgrades
Lockheed's development roadmap extends until 2021, including a block 6 engine improvement in 2019. The aircraft are expected to be upgraded throughout their operational lives.
Design
The F-35 appears to be a smaller, slightly more conventional, single-engine sibling of the sleeker, twin-engine Lockheed Martin F-22 Raptor, and indeed drew elements from it. The exhaust duct design was inspired by the General Dynamics Model 200 design, which was proposed for a 1972 supersonic VTOL fighter requirement for the Sea Control Ship. For specialized development of the F-35B STOVL variant, Lockheed consulted with the Yakovlev Design Bureau, purchasing design data from their development of the Yakovlev Yak-141 "Freestyle". Although several experimental designs have been built and tested since the 1960s including the navy's unsuccessful Rockwell XFV-12, the F-35B is to be the first operational supersonic, STOVL stealth fighter.
The F-35 has a maximum speed of over Mach 1.6. With a maximum takeoff weight of 60,000 lb (27,000 kg), the Lightning II is considerably heavier than the lightweight fighters it replaces. In empty and maximum gross weights, it more closely resembles the single-seat, single-engine Republic F-105 Thunderchief, which was the largest single-engine fighter of the Vietnam war era. The F-35's modern engine delivers over 60 percent more thrust in an aircraft of the same weight so that in thrust to weight and wing loading it is much closer to a comparably equipped F-16.
Acquisition deputy to the assistant secretary of the Air Force, Lt. Gen. Mark D. "Shack" Shackelford has said that the F-35 is designed to be America's "premier surface-to-air missile killer and is uniquely equipped for this mission with cutting edge processing power, synthetic aperture radar integration techniques, and advanced target recognition."
Some improvements over current-generation fighter aircraft are:
- Durable, low-maintenance stealth technology, using structural fibre mat instead of the high-maintenance coatings of legacy stealth platforms;
- Integrated avionics and sensor fusion that combine information from off- and on-board sensors to increase the pilot's situational awareness and improve target identification and weapon delivery, and to relay information quickly to other command and control (C2) nodes;
- High speed data networking including IEEE 1394b and Fibre Channel. (Fibre Channel is also used on Boeing's Super Hornet.)
- The Autonomic Logistics Global Sustainment (ALGS), Autonomic Logistics Information System (ALIS) and Computerized maintenance management system (CMMS) are to help ensure aircraft uptime with minimal maintenance manpower. The Pentagon has moved to open the up competitive bidding by other companies. This was after Lockheed admitted that instead of costing twenty percent less than the F-16 per flight hour, the F-35 would actually cost twelve percent more. Though the ALGS is intended to reduce maintenance costs, Lockheed Martin disagrees with including the cost of this system in the aircraft ownership calculations. USMC have implemented a workaround for a cyber vulnerability in the system.
- Electrohydrostatic actuators run by a power-by-wire flight-control system.
- A modern and updated flight simulator, which may be used for a greater fraction of pilot training in order to reduce the costly flight hours of the actual aircraft.
- Lightweight, powerful and volatile Lithium-ion batteries similar to those that have grounded the Boeing 787 Dreamliner fleet. These are required to provide power to run the control surfaces in an emergency, and have been strenuously tested.
Lockheed Martin claims the F-35 is intended to have close and long-range air-to-air capability second only to that of the F-22 Raptor. The company has suggested that the F-35 could also replace the USAF's F-15C/D fighters in the air superiority role and the F-15E Strike Eagle in the ground attack role, but it does not have the range or payload of either F-15 model. The F-35A does carry a similar air-to-air armament as the conceptual Boeing F-15SE Silent Eagle when both aircraft are configured for low observable operations and has over 80 percent of the larger aircraft's combat radius, under those conditions.
Lockheed Martin has said that the F-35 has the advantage over the F-22 in basing flexibility and "advanced sensors and information fusion".
Structural composites in the F-35 are 35% of the airframe weight (up from 25% in the F-22). The majority of these are bismaleimide (BMI) and composite epoxy material. The F-35 will be the first mass produced aircraft to include structural nanocomposites, namely carbon nanotube reinforced epoxy.
The F-35 program has learned from the corrosion problems that the F-22 had when it was first introduced in 2005. The F-35 uses a gap filler that causes less galvanic corrosion to the skin, is designed with fewer gaps in its skin that require gap filler, and has better drainage.
A United States Navy study found that the F-35 will cost 30 to 40 percent more to maintain than current jet fighters. This does not account for inflation over the 30+ years of the F-35 program. A Pentagon study found that it may cost $1 trillion to maintain the entire fleet over its lifetime.
The relatively short 35 foot wingspan of the A and B variants is set by the F-35B's requirement to fit inside the Navy's current amphibious assault ship elevators. The F-35C's longer wing is considered to be more fuel efficient.
Engines
The F-35's main engine is the Pratt & Whitney F135. The General Electric/Rolls-Royce F136 was under development as an alternative engine until December 2011 when the manufacturers canceled work on it. The F135/F136 engines are not designed to supercruise in the F-35, but the F-35 can achieve a limited supercruise of Mach 1.2 for 150 miles. The STOVL versions of both power plants use the Rolls-Royce LiftSystem, designed by Lockheed Martin and developed to production by Rolls-Royce. This system is more like the Russian Yak-141 and German VJ 101D/E than the preceding generation of STOVL designs, such as the Harrier Jump Jet in which all of the lifting air went through the main fan of the Rolls-Royce Pegasus engine.
The Lift System is composed of a lift fan, drive shaft, two roll posts and a "Three Bearing Swivel Module" (3BSM). The 3BSM is a thrust vectoring nozzle which allows the main engine exhaust to be deflected downward at the tail of the aircraft. The lift fan is near the front of the aircraft and provides a counterbalancing thrust using two counter-rotating blisks. It is powered by the engine's low-pressure (LP) turbine via a drive shaft and gearbox. Roll control during slow flight is achieved by diverting unheated engine bypass air through wing-mounted thrust nozzles called Roll Posts. Like lift engines, the added lift fan machinery increases payload capacity during vertical flight, but is dead weight during horizontal flight. The cool exhaust of the fan also reduces the amount of hot, high-velocity air that is projected downward during vertical take off, which can damage runways and aircraft carrier decks.
To date, F136 funding has come at the expense of other parts of the program, reducing the number of aircraft built and increasing their costs. The F136 team has claimed that their engine has a greater temperature margin which may prove critical for VTOL operations in hot, high altitude conditions.
Pratt & Whitney is also testing higher thrust versions of the F135, partly in response to GE's claims that the F136 is capable of producing more thrust than the 43,000 lbf (190 kN) supplied by early F135s. The F135 has demonstrated a maximum thrust of over 50,000 lbf (220 kN) during testing. The F-35's Pratt & Whitney F135 is the most powerful engine ever installed in a fighter aircraft.
The F135 is the second (radar) stealthy afterburning jet engine and like the Pratt & Whitney F119 from which it was derived, has suffered from pressure pulsations in the afterburner at low altitude and high speed or "screech". In both cases this problem was fixed during development of the fighter program.
Turbine bearing health in the engine will be monitored with thermoelectric powered wireless sensors.
Armament
The F-35A includes a GAU-22/A, a four-barrel version of the GAU-12 Equalizer 25 mm cannon. The cannon is mounted internally with 182 rounds for the F-35A or in an external pod with 220 rounds for the F-35B and F-35C. The gun pod for the B and C variants will have stealth features. The Terma A/S multi-mission pod (MMP) could be used for different equipment in the future for all three variants, such as electronic warfare equipment, reconnaissance equipment, or possibly a rearward-facing radar.
It has two internal weapons bays, and external hardpoints that can mount four underwing pylons and two near wingtip pylons. The two outer hardpoints can only carry pylons for the AIM-9X Sidewinder and AIM-132 ASRAAM short-range air-to-air missiles (AAM). The other pylons can carry the AIM-120 AMRAAM BVR AAM, Storm Shadow air-launched cruise missile, AGM-158 Joint Air to Surface Stand-off Missile (JASSM) cruise missile, and guided bombs. The external pylons can carry missiles, bombs, and fuel tanks at the expense of reduced stealth. An air-to-air load of eight AIM-120s and two AIM-9s is possible using internal and external weapons stations; a configuration of six 2,000 lb (910 kg) bombs, two AIM-120s and two AIM-9s can also be arranged.
There are a total of four weapons stations between the two internal weapons bays. Two of these can carry air-to-ground bombs up to 2,000 lb (910 kg) in A and C models, or two bombs up to 1,000 lb (450 kg) in the B model. The other two stations are for smaller weapons, normally expected to be air-to-air missiles. The weapon bays can carry AIM-120 AMRAAM, AIM-132 ASRAAM, the Joint Direct Attack Munition (JDAM), the Joint Stand off Weapon (JSOW), Brimstone anti-armor missiles, and Cluster Munitions (WCMD).
Lockheed Martin states that the weapons load can also be configured as all-air-to-ground or all-air-to-air. The company has suggested that a Block 5 version will carry three weapons per bay instead of two, replacing the heavy bomb with two smaller weapons such as AIM-120 AMRAAM air-to-air missiles. Upgrades are to allow each weapons bay to carry four GBU-39 Small Diameter Bombs (SDB) for A and C models, or three in F-35B. Another option is four GBU-53/B Small Diameter Bomb IIs in each bay on all F-35 variants. An F-35 has been loaded with four SDB II bombs alongside an AMRAAM missile, successfully validating that the SDB II is compatible with the F-35 and gives adequate clearance in sweeps of inboard and outboard bay doors. The MBDA Meteor air-to-air missile is currently being adapted to fit four internally in the missile spots and may be integrated into the F-35. A modified Meteor design with smaller tailfins for the F-35 was revealed in September 2010. The United Kingdom had originally planned to put up to four AIM-132 ASRAAM internally but this has been changed to carry two internal and two external ASRAAMs. The external ASRAAMs are planned to be carried on "stealthy" pylons to increase the F-35's radar cross section slightly; the missile allow attacks to slightly beyond visual range without using radar that might alert the target.
Norway and Australia are funding a program to adapt the Naval Strike Missile (NSM) to fit the internal bays of the F-35. This will be a multi-role version, named the Joint Strike Missile (JSM), and will be the only cruise missile to fit the internal bays. Studies have shown that the F-35 would be able to carry two of these internally, while four additional missiles could be carried externally. The missile has an expected range in excess of 150 nmi (278 km).
Solid state lasers were being developed as optional weapons for the F-35 as of 2002. The F-35 is expected to take on the Wild Weasel mission, but there are no planned anti-radiation missiles for internal stealthy carriage. The B61 nuclear bomb was scheduled for deployment in 2017, but delays in the F-35 program may delay this. It is now expected to be deployable in the early 2020s.
Stealth and signatures
The F-35 has been designed to have a low radar cross section primarily due to the shape of the aircraft and the use of stealthy materials used in construction, including fibre-mat. Unlike the previous generation of fighters, the F-35 was designed with a shape for very-low-observable characteristics.
The Teen Series of fighters (F-15, F-16, F/A-18) were notable for always carrying large external fuel tanks, but in order to avoid negating its stealth characteristics the F-35 must fly most missions without external fuel tanks. Unlike the F-16 and F/A-18, the F-35 lacks leading edge extensions and instead uses stealth-friendly chines for vortex lift in the same fashion as the SR-71 Blackbird. The small bumps just forward of the engine air intakes form part of the diverterless supersonic inlet (DSI) which is a simpler, lighter means to ensure high-quality airflow to the engine over a wide range of conditions. These inlets also crucially improve the aircraft's very-low-observable characteristics.
In spite of being smaller than the F-22, the F-35 has a larger radar cross section. It is said to be roughly equal to a metal golf ball rather than the F-22's metal marble. The F-22 was designed to be difficult to detect by all types of radars and from all directions. The F-35 on the other hand manifests its lowest radar signature from the frontal aspect because of compromises in design. Its surfaces are shaped to best defeat radars operating in the X and upper S band, which are typically found in fighters, surface-to-air missiles and their tracking radars; the aircraft would be easier to detect using other radar frequencies. Because the shape of the aircraft is so important to its radar cross section (RCS), special care must be taken to maintain the "outer mold line" during production. Ground crews require Repair Verification Radar (RVR) test sets in order to verify the RCS of the aircraft after performing repairs, which was not a concern for previous generations of non-stealth fighters.
As well as being radar stealthy, the F-35 has infrared and visual signature reduction incorporated.
In late 2008 the air force revealed that the F-35 would be about twice as loud at takeoff as the McDonnell Douglas F-15 Eagle and up to four times as loud during landing. As a result, residents near Luke Air Force Base, Arizona and Eglin Air Force Base, Florida, possible home bases for the jet, requested that the air force conduct environmental impact studies concerning the F-35's noise levels. The city of Valparaiso, Florida, adjacent to Eglin AFB, threatened in February 2009 to sue over the impending arrival of the F-35s, but this lawsuit was settled in March 2010. It was reported in March 2009 that testing by Lockheed Martin and the Royal Australian Air Force revealed that the F-35 was not as loud as first reported, being "only about as noisy as an F-16 fitted with a Pratt & Whitney F100-PW-200 engine" and "quieter than the Lockheed Martin F-22 Raptor and the Boeing F/A-18E/F Super Hornet." According to an acoustics study done by Lockheed Martin and the U.S. Air Force, the noise levels of the F-35 are found to be comparable to the F-22 Raptor and F/A-18E/F Super Hornet. And a USAF environmental impact study found that replacing the F-16s with F-35s at Tucson International Airport would subject more than 21 times as many residents to extreme noise levels.
Cockpit
The F-35 features a full-panel-width "panoramic cockpit display" (PCD) glass cockpit, with dimensions of 20 by 8 inches (50 by 20 centimeters). A cockpit speech-recognition system ( Direct Voice Input) provided by Adacel is planned to improve the pilot's ability to operate the aircraft over the current-generation interface. The F-35 will be the first U.S. operational fixed-wing aircraft to use this system, although similar systems have been used in AV-8B and trialled in previous U.S. jets, particularly the F-16 VISTA.
A helmet-mounted display system (HMDS) will be fitted to all models of the F-35. A helmet-mounted cueing system is already in service with the F-15s, F-16s and F/A-18s. While some fighters have offered HMDS along with a head up display (HUD), this will be the first time in several decades that a front line tactical jet fighter has been designed without a HUD. The F-35 is equipped with a right-hand HOTAS side stick controller.
The Martin-Baker US16E ejection seat is used in all F-35 variants. The US16E seat design balances major performance requirements, including safe-terrain-clearance limits, pilot-load limits, and pilot size. It uses a twin-catapult system that is housed in side rails. The F-35 uses a derivative version of the oxygen system that has been implicated in hypoxia incidents on board the F-22. But the F-35 does not fly as high or as fast as the F-22; its flight profile is similar to other fighters that use such systems routinely.
Sensors and avionics
The F-35's sensor and communications suite is intended for situational awareness, command-and-control and network-centric warfare capability. The main sensor on board the F-35 is its AN/APG-81 AESA-radar, designed by Northrop Grumman Electronic Systems. It is augmented by the Electro-Optical Targeting System (EOTS) mounted under the nose of the aircraft, designed by Lockheed Martin. This gives the same capabilities as the Lockheed Martin Sniper XR without making the aircraft more easily detectable.
Six additional passive infrared sensors are distributed over the aircraft as part of Northrop Grumman's AN/AAQ-37 distributed aperture system (DAS), which acts as a missile warning system, reports missile launch locations, detects and tracks approaching aircraft spherically around the F-35, and replaces traditional night vision goggles for night operations and navigation. All DAS functions are performed simultaneously, in every direction, at all times. The F-35's Electronic Warfare systems are designed by BAE Systems and include Northrop Grumman components. Some functions such as the Electro-Optical Targeting System and the Electronic Warfare system are not usually found integrated on fighters.
The AN/ASQ-239 (Barracuda) system is an improved version of the AN/ALR-94 EW suite on the F-22. The AN/ASQ-239 provides sensor fusion of RF and IR tracking functions, basic radar warning, multispectral countermeasures for self-defense against threat missiles, situational awareness and electronic surveillance. It uses 10 RF antennae over the leading and trailing edges of the wing leading and trailing edges of the horizontal tail.
The communications, navigation and identification (CNI) suite is designed by Northrop Grumman and includes the Multifunction Advanced Data Link (MADL). The F-35 will be the first jet fighter with sensor fusion that combines radio frequency and IR tracking for continuous target detection and identification in all directions which is shared via MADL to other platforms without compromising low observability. The F-35 also includes the non-stealthy Link 16 for communications with legacy systems for missions including Close air support.
The F-35 has been designed with synergy between sensors as a specific requirement, with the "senses" of the aircraft expected to provide a more cohesive picture of the reality around it, and be available in principle for use in any possible way, and any possible combination with one another. All of the sensors feed directly into the main processors. For example the AN/APG-81 functions not just as a multi-mode radar, but also as part of the aircraft's electronic warfare system. Northrop Grumman is offering the APG-81 as an upgrade for legacy aircraft, but because the "back end processing" on the F-35 is done in software on the main processors, the upgrade version requires their Scalable Agile Beam Radar electronics to operate on other aircraft.
Unlike previous aircraft, such as the F-22, much of the new software for the F-35 is written in C and C++, because of programer availability. Much Ada83 code is reused from the F-22. The Integrity DO-178B real-time operating system (RTOS) from Green Hills Software runs on COTS Freescale PowerPC processors. The final Block 3 software for the F-35 is planned to have 8.6 million lines of software code. The scale of the program has led to a software crisis as officials continue to discover that additional software needs to be written. General Norton Schwartz has said that the software is the biggest factor that might delay the USAF's initial operational capability, which is now scheduled for April 2016. Michael Gilmore, Director of Operational Test & Evaluation, has written that, "the F-35 mission systems software development and test is tending towards familiar historical patterns of extended development, discovery in flight test, and deferrals to later increments."
The F-35's electronic warfare systems are intended to detect hostile aircraft, then scan them with the electro-optical system to allow the pilot to engage or evade the opponent before the F-35 is detected. The CATbird avionics testbed for the F-35 program has proved capable of detecting and jamming F-22 radars.
The F-35 was previously considered a platform for the Next Generation Jammer, but attention has shifted to the use of unmanned platforms.
Helmet-mounted display system
The F-35 does not need to be physically pointing at its target for weapons to be successful. Sensors can track and target a nearby aircraft from any orientation, provide the information to the pilot through his helmet (and therefore visible no matter which way the pilot is looking), and provide the seeker-head of a missile with sufficient information. Recent missile types provide a much greater ability to pursue a target regardless of the launch orientation, called "High Off-Boresight" capability, although the speed and direction in which the munition is launched affect the effective range of the weapon. Sensors use combined radio frequency and infra red (SAIRST) to continually track nearby aircraft while the pilot's helmet-mounted display system (HMDS) displays and selects targets. The helmet system replaces the display-suite-mounted head-up display used in earlier fighters.
The F-35's systems provide the edge in the "observe, orient, decide, and act" OODA loop; stealth and advanced sensors aid in observation (while being difficult to observe), automated target tracking helps in orientation, sensor fusion simplifies decision making, and the aircraft's controls allow the pilot to keep their focus on the targets, rather than the controls of their aircraft.
The problems with the current Vision Systems International helmet-mounted display led Lockheed Martin on 1 March 2011 to issue a draft specification for proposals for an alternative . The alternative system will be based on Anvis-9 night vision goggles. It will be supplied by BAE systems. The BAE system does not yet include all the features of the VSI helmet and if successful will have the remaining features incorporated. Use of the BAE system would also require a cockpit redesign.
In 2011, Lockheed granted VSI a contract to fix the vibration, jitter, night-vision and sensor display problems in their helmet-mounted display. The improved displays are expected to be delivered in the third quarter of 2013. One of the potential improvements is to replace Intevac’s ISIE-10 day/night camera located in the helmet with their ISIE-11 model which will improve the resolution from 1280x1024 to 1600x1200 pixels. By October 2012, Lockheed said it had made progress in resolving technical issues of the helmet-mounted display, citing positive reports from night flying tests. Night vision performance was the "only real question" left on the helmet, and it was questioned whether the helmet system would allow pilots to see well enough at night to carry out precision tasks.
Maintenance
The program's maintenance concept is for any F-35 to be maintained in any F-35 maintenance facility and that all F-35 parts in all bases will be globally tracked and shared as needed. The commonality between the different variants has allowed the USMC to create their first aircraft maintenance Field Training Detachment to directly apply the lessons of the USAF to their F-35 maintenance operations.
The aircraft has been designed for ease of maintenance, with 95% of all field replaceable parts "one deep" where nothing else has to be removed to get to the part in question. For instance the ejection seat can be replaced without removing the canopy, the aircraft uses low-maintenance electro-hydrostatic actuators instead of hydraulic systems and an all-composite skin without the fragile coatings found on earlier stealth aircraft.
The F-35 has received good reviews from pilots and maintainers, suggesting it is performing better than its predecessors did at a similar stage of development. The stealth type has proved relatively stable from a maintenance standpoint. Part of the improvement is attributed to better maintenance training, as F-35 maintainers have received far more extensive instruction at this early stage of the program than on the F-22 Raptor. The F-35's stealth coatings are much easier to work with than those used on the Raptor. Cure times for coating repairs are lower and many of the fasteners and access panels are not coated, further reducing the workload for maintenance crews. Some of the F-35's radar-absorbent materials are baked into the jet's composite skin, which means its stealthy signature is not easily degraded. It is still harder to maintain (due to its stealth) than fourth-generation aircraft.
Operational history
Testing
The first F-35A (designated AA-1) was rolled out in Fort Worth, Texas, on 19 February 2006, before undergoing ground testing at Naval Air Station Joint Reserve Base Fort Worth in late 2006. In September 2006 the first engine run of the F135 in an airframe and tests were completed. On 15 December 2006, the F-35A completed its maiden flight. A modified Boeing 737–300, the Lockheed CATBird is used as an avionics test-bed inside which are racks holding all of F-35's avionics, as well as a complete F-35 cockpit.
The first F-35B (designated BF-1) made its maiden flight on 11 June 2008, piloted by BAE Systems' test pilot Graham Tomlinson. In-flight testing of the variant's STOVL propulsion system began on 7 January 2010. The F-35B's first hover was on 17 March 2010, followed by its first vertical landing the next day. During a test flight on 10 June 2010, the F-35B became the second STOVL aircraft to achieve supersonic speeds after the X-35B. In January 2011, Lockheed Martin reported it had solved a problem with the aluminium bulkhead used on the F-35B which had cracked during ground testing. The F-35B suffered from another bulkhead crack the next year, needing another heavier replacement part to be designed.
F-35B tests on USS Wasp in 2011 | |
![]() |
|
![]() |
|
![]() |
By June 2009 many of the initial flight test targets had been accomplished, but the F-35 testing program was falling behind schedule. During the previous year, a Pentagon Joint Estimate Team (JET) estimated that the program was two years behind the latest public schedule, and a revised estimate in 2009 predicted a 30-month delay. Due to these test delays, planned production numbers were reduced by 122 aircraft through 2015 to provide 2.8 billion in additional funds for development; internal memos suggested that the official timeline would be extended by 13 months The success of the JET has led Ashton Carter to call for more such teams for other poorly performing Pentagon projects.
Nearly 30 percent of the test flights have required more than routine maintenance to get the aircraft flying again. As of March 2010, the F-35 program had used a million more man-hours than predicted and flight testing is expected to result in further design changes. The United States Navy has projected that lifecycle costs over a fleet life of 65 years for all of the American F-35s will be $442 billion higher than the U.S. Air Force has projected. The delay in the F-35 program is expected to lead to a shortfall of around 100 jet fighters in the Navy/Marines team. Given careful management, service life extension of the Marines' F/A-18s, and more burdens placed on Navy fighters, it may be possible to reduce this shortfall.
The F-35C's maiden flight took place on 7 June 2010, also at NAS Fort Worth JRB. A total of 11 U.S. Air Force F-35s arrived in fiscal year 2011. On 9 March 2011 all F-35s were grounded after a dual generator failure and oil leak in flight. The problem was found to be the result of faulty maintenance.
In June 2011, the F-35's sensors (radar and DAS) were tested in an exercise named Northern Edge 2011. Navy Commander Erik Etz, an official from the F-35 JSF Program Office, said the rigorous testing of both sensors during Northern Edge 2011 served as a significant risk-reduction step for the F-35 JSF program.
From 3–18 August 2011, the F-35 fleet was grounded while the Joint Program Office investigated an electrical system failure on test aircraft, F-35A AF-4 during ground tests. The Honeywell-built integrated power package (IPP) failed during a standard engine test following a maintenance check on 2 August at Edwards Air Force Base. The IPP combines the functions of an environment control unit, engine starter and back-up power generator. The JPO was assessing the impact of the grounding on the schedule for the system development and demonstration phase, but the latest version of the schedule included margin for unexpected problems. On 10 August 2011, ground operations for the F-35 Program were re-instituted while the investigation was ongoing. Preliminary root cause inquiries indicated that a control valve did not function properly, which in turn led to the IPP failure. Further reviews were required prior to lifting the suspension of flight operations for the F-35. On 18 August 2011, the flight ban was lifted for 18 of the 20 fighters. Two aircraft based at Eglin Air Force Base in Florida remained grounded because they lacked the monitoring systems used in developmental test aircraft to detect problems in flight. The IPP suffered another software related incident in 2013, but this caused no additional disruption because the fleet was already grounded due to engine issues.
On 25 October 2011 the F-35A reached its designed top speed of Mach 1.6 for the first time. Further testing demonstrated Mach 1.61 and 9.9g. During testing in 2011, all eight landing tests of the F-35C tail hook failed to catch the arresting wire; the hook design is being modified. In October 2011, two F-35B VTOL aircraft conducted three weeks of initial sea trials aboard USS Wasp (LHD-1).
On 15 August 2012, an F-35B completed air start tests, which involved shutting down and restarting the engine while in flight; the F-35A had previously completed these tests.
During the fourth quarter of 2012, weapons separation tests were performed. On 6 October 2012, the F-35A dropped its first bomb, followed three days later by the AIM-120 AMRAAM. On 28 November 2012, an F-35C test aircraft performed a total of eleven weapon releases, ejecting a GBU-31 JDAM and GBU-12 Paveway from its weapons bay in the first ground weapons ejections for the F-35C.
On 16 November 2012, the U.S. Marines received the first F-35B at MCAS Yuma, and the VMFA(AW)-121 unit is to be redesignated from a Boeing F/A-18 Hornet unit to an F-35B squadron. A February 2013 Time article revealed that Marine pilots are not allowed to perform a vertical landing – the maneuver is deemed too dangerous, and it is reserved only for Lockheed test pilots.
On 18 January 2013, the F-35B variant was grounded after the failure of a fueldraulic line in the aircraft's propulsion system on 16 January prior to a conventional takeoff. The problem was traced an “improperly crimped” fluid line manufactured by Stratoflex. The Pentagon cleared all 25 F-35B aircraft to resume flight tests on 12 February 2013.
On 11 February 2013, an F-35A completed its final test mission for clean wing flutter. Flutter testing demonstrated it was clear of flutter at speeds up to Mach 1.6 with weapon bay doors open and closed.
On 22 February 2013, the U.S. Department of Defense grounded the entire fleet of 51 F-35s after the discovery of a cracked turbine blade in a U.S. Air Force F-35A at Edwards Air Force Base. On 28 February 2013, the Defense Department lifted the grounding after an investigation concluded that the cracks in that particular engine resulted from stressful testing, including excessive heat for a prolonged period during flight, and did not reflect a fleetwide problem.
Training
In 2011, the Director of Operational Test and Evaluation warned that the USAF's plan to start unmonitored flight training "risks the occurrence of a serious mishap". The leaders of the United States Senate Committee on Armed Services called on Defense Secretary Leon Panetta to address the issue. The flights began in September 2012.
The F-35A and F-35B were cleared for flight training in early 2012. A military flight release for the F-35A was issued on 28 February 2012. Currently the aircraft are restricted to basic maneuvers with no tactical training allowed.
On 24 August 2012, an F-35 flew its 200th sortie while at Eglin Air Force Base, flown by a Marine pilot. The pilot said, "The aircraft have matured dramatically since the early days. The aircraft are predictable and seem to be maintainable, which is good for the sortie production rate. Currently, the flight envelope for the F-35 is very, very restricted, but there are signs of improvement there too." The F-35s at the base no longer need to fly with a chase aircraft and are operating in a normal two-ship element.
On 21 August 2012, J. Michael Gilmore wrote that he would not approve the Operational Test and Evaluation master plan until his concerns about electronic warfare testing, budget and concurrency were addressed. On 7 September 2012, the Pentagon failed to approve a comprehensive operational testing plan for the F-35. Instead, on 10 September 2012, the USAF started an operational utility evaluation (OUE) of the F-35A variant. This was scheduled to last 65 training days and was to evaluate the entire air vehicle system, including logistical support and maintenance, maintenance training, pilot training, and pilot execution. Four pilots were part of the OUE. The U.S. Navy and Marines do not yet have an OUE scheduled for their respective versions. By 1 October, the OUE was reported as "proceeding smoothly." The pilots went through academics and started their normal operations simulators. Flying began on 26 October. By 9 November 20 out 24 planned flight sorties had been completed. The OUE was completed on 14 November with the 24th flight. The four pilots completed six flights each, along with simulator work and an academics phase. A report on the readiness of the F-35 and the training syllabus was compiled. The Air Force decided it would begin pilot training in January 2013.
As the F-35 is a software defined aircraft, the maintenance personnel have found that many deficiencies identified can be fixed by simply rebooting the software through an aircraft restart.
During the Low Rate Initial Production (LRIP) phase of the aircraft, the U.S. had taken a tri-service approach to developing tactics and procedures for the F-35 using flight simulators. Because of this, the concept of operations and employment for it were already being developed before it was in service. The simulators helped discover technical problems used to refine further designs. Computers also flew some simulated flights to test the effectiveness of the aircraft's flight controls.
Pilot training of the Air Force's F-35A Lightning II started in January 2013 at Eglin Air Force Base. The training will include six classes of six students throughout the year, with a full capacity of 100 military pilots and 2,100 maintainer students.
Procurement and international participation
While the United States is the primary customer and financial backer, the United Kingdom, Italy, the Netherlands, Canada, Turkey, Australia, Norway and Denmark have agreed to contribute US$4.375 billion toward the development costs of the program. Total development costs are estimated at more than US$40 billion (underwritten largely by the United States), while the purchase of an estimated 2,400 aircraft is expected to cost an additional US$200 billion. The initial plan was that the nine major partner nations would acquire over 3,100 F-35s through 2035. Sales to partner nations are made through the Pentagon's Foreign Military Sales program.
There are three levels of international participation. The levels generally reflect the financial stake in the program, the amount of technology transfer and subcontracts open for bid by national companies, and the order in which countries can obtain production aircraft. The United Kingdom is the sole "Level 1" partner, contributing US$2.5 billion, which was about 10% of the planned development costs under the 1995 Memorandum of Understanding that brought the UK into the project. Level 2 partners are Italy, which is contributing US$1 billion; and the Netherlands, US$800 million. Level 3 partners are Turkey, US$195 million; Canada, US$160 million; Australia, US$144 million; Norway, US$122 million and Denmark, US$110 million. Israel and Singapore have joined as Security Cooperative Participants (SCP). Japan announced on 20 December 2011 its intent to purchase 42 F-35s with deliveries beginning in 2016 to replace F-4 Phantom II aircraft. The country wants at least 38 of the F-35s to be assembled in Japan.
By February 2012, many changes had occurred in the F-35 order book. Italy became the first country to announce it was reducing its overall fleet procurement, cutting its buy from 131 to 90 aircraft. Other nations reduced initial purchases or delayed orders, while still intending to purchase the same final numbers. The United States canceled the initial purchase of 13 F-35s and postponed orders for another 179. Britain cut its initial order and delayed a decision on future orders. Australia decided to buy the Boeing F/A-18E/F Super Hornet as an interim measure until the F-35 is ready. Turkey also cut its initial order of four aircraft to two, but confirmed plans to purchase 100 F-35As. Turkey will buy four F-35s to be delivered in 2015 and 2016, while the order may be increased from 100 to 120 aircraft. All of these changes in procurement resulted in increased prices for the aircraft and thus increased the likelihood of further procurement cuts. The Netherlands planned to buy 85 aircraft, but is considering buying 68 in 2013.
The Auditor General of Canada Michael Ferguson published a report on 3 April 2012 outlining problems with Canada's procurement of the jet, including misinformation about the final cost of the jet. According to comments Ferguson made 5 April, the government knowingly understated the final price for Canada's 65 jets by $10 billion, igniting heated debate over the purchase. Canada's Conservative government had previously been saying it would not reduce its order, claiming an anticipated $75–80 million unit cost per fighter, and budgeting for cost overruns of ~10%. By 6 April the Canadian procurement was being termed a "scandal" and "fiasco" by the media and now faces a full review to determine whether Canada will buy any F-35s. On 13 December 2012, in a scathing editorial published by CBC News, journalist Brian Stewart termed the F-35 project a "global wrecking ball" due to its run-away costs and lack of affordability for many participating nations.
Variants
The F-35 is being built in three different main versions to suit various combat missions.
F-35A
The F-35A is the conventional takeoff and landing ( CTOL) variant intended for the U.S. Air Force and other air forces. It is the smallest, lightest F-35 version and is the only variant equipped with an internal cannon, the GAU-22/A. This 25 mm cannon is a development of the GAU-12 carried by the USMC's AV-8B Harrier II. It is designed for increased effectiveness against ground targets compared to the 20 mm M61 Vulcan cannon carried by other USAF fighters.
The F-35A is expected to match the F-16 in maneuverability and instantaneous and sustained high-g performance, and outperform it in stealth, payload, range on internal fuel, avionics, operational effectiveness, supportability, and survivability. It is expected to match an F-16 that is carrying the usual external fuel tank in acceleration performance. It also has an internal laser designator and infrared sensors, equivalent to the Sniper XR pod carried by the F-16, but built in to reduce radar cross section.
The A variant is primarily intended to replace the USAF's F-16 Fighting Falcon. It was also intended to replace the A-10 Thunderbolt II starting in 2028.
The F-35A can be outfitted with either of the two main air to air refueling types, which was a consideration in the Canadian purchase, and a deciding factor in the cost for the Japanese purchase.
F-35B
The F-35B is the short takeoff and vertical landing ( STOVL) variant of the aircraft. Similar in size to the A variant, the B sacrifices about a third of the other version's fuel volume to make room for the vertical flight system. Takeoffs and landing with vertical flight systems are by far the riskiest, and in the end, a decisive factor in design. Like the AV-8B Harrier II, the B’s guns will be carried in a ventral pod. Whereas the F-35A is stressed to 9 g, the F-35B is stressed to 7 g. The F-35B was unveiled at Lockheed Martin's Fort Worth plant on 18 December 2007, and the first test flight was on 11 June 2008.
Unlike the other variants, because it can land vertically the F-35B has no landing hook. The "STOVL/HOOK" button in the cockpit initiates conversion instead of dropping the hook. The F-35B sends jet thrust directly downwards during vertical takeoffs and landing and the nozzle is being redesigned to spread the output out in an oval rather than a small circle so as to limit damage to asphalt and ship decks. The variant's three-bearing swivel nozzle that directs the full thrust of the afterburning jet engine is moved by a “fueldraulic” actuator, using pressurized jet fuel.
The United States Marine Corps plans to purchase 340 F-35Bs, to replace all current inventories of the F/A-18 Hornet (A, B, C and D-models), and AV-8B Harrier II in the fighter, and attack roles. The Marines are planning to use the F-35B from "unimproved surfaces at austere bases" and are preparing landing spots with "special, high-temperature concrete designed to handle the heat from the JSF".
The Royal Air Force and Royal Navy plan to use the F-35B to replace their Harrier GR9s, which were retired in 2010. One of the Royal Navy requirements for the F-35B design was a Shipborne Rolling and Vertical Landing (SRVL) mode to increase the maximum landing weights for carried weapons via wing lift. In October 2010, the UK announced plans to order to the CATOBAR F-35C variant instead, but in May 2012 the UK reverted back to purchasing the F-35B, citing the cost of equipping the UK's new aircraft carriers for the F-35C. On 19 July 2012 the Defence Secretary Philip Hammond, in a speech in the USA, indicated that the UK would initially receive 48 F-35B and would announce at a later date what the final numbers will be.
The Italian Navy is preparing Grottaglie Air Station for future operations with the F-35B. The Italian Navy is to receive 22 aircraft between 2014 and 2021, with its Cavour aircraft carrier set to be modified to operate them by 2016.
Commandant of the U.S. Marine Corps, General James Amos has said that, in spite of its increasing costs and schedule delays, there is no plan B to substitute for the F-35B. The F-35B is larger than the aircraft it replaces, which required the USS America (LHA-6) to be designed without needed well deck capabilities. In 2011, the USMC and USN signed an agreement that the USMC will purchase 340 F-35B and 80 F-35C fighters while the USN will purchase 260 F-35C fighters. The five squadrons of USMC F-35Cs will be assigned to the Navy carriers while the USMC F-35Bs will be used on amphibious ships and ashore.
On 6 January 2011, Gates said that the 2012 budget would call for a two-year pause in F-35B production during which the aircraft may be redesigned, or canceled if unsuccessful. The probation was ended by Defense Secretary Leon Panetta in January 2012 because of progress made over the past year.
Lockheed Martin executive vice president Tom Burbage and former Pentagon director of operational testing Tom Christie have said that most of the delays in the total program have been due to issues with the F-35B, which forced massive redesigns on the other versions.
The USMC intends to declare Initial Operational Capability with about 50 F-35s running interim Block 2B software in the 2014 to 2015 timeframe.
Lockheed Martin Vice President Steve O’Bryan has said that most F-35B landings will be purely conventional in order to reduce stress on the vertical lift components. Conventional operations also reduce the risk of self-induced foreign object damage.
On 3 October 2011, the F-35B began its initial sea-trials by performing a vertical landing on the deck of the amphibious assault ship USS Wasp.
The USAF considered replacing the A-10 with the F-35B, but will not do so because the F-35B will not be able to generate sufficient sorties.
F-35C
Compared to the F-35A, the F-35C carrier variant features larger wings with foldable wingtip sections, larger wing and tail control surfaces for improved low-speed control, stronger landing gear for the stresses of carrier arrested landings, a twin-wheel nose gear, and a stronger tailhook for use with carrier arrestor cables. The larger wing area allows for decreased landing speed while increasing both range and payload.
The United States Navy will use the F-35C carrier variant. It intends to buy 480 F-35Cs to replace the F/A-18A, B, C, and D Hornets. The F-35C will also serve as a very-low-observable complement to the Super Hornet. On 27 June 2007, the carrier variant completed its Air System Critical Design Review (CDR). This allows the first two functional prototype F-35C units to be produced. The C variant is expected to be available beginning in 2014. The first F-35C was rolled out on 29 July 2009. The United States Marine Corps will also purchase 80 F-35Cs, enough for five marine fighter-attack squadrons, for use with navy carrier air wings in a joint service agreement signed on 14 March 2011.
On 6 November 2010, the first F-35C arrived at Naval Air Station Patuxent River. At the time, it was determined that the replacement engines for at-sea repair are too large to be transported by current underway replenishment systems. In 2011, the F-35Cs were grounded for six days because of a software error in the code that was intended to keep the wings from folding in mid-flight. On 27 July 2011, the F-35C test aircraft CF-3 completed its first steam catapult launch during a test flight in Naval Air Engineering Station Lakehurst. The TC-13 Mod 2 test steam catapult, representative of current fleet technology, was used. In addition to the catapult launches at varying power levels, the integrated test team is to execute a test plan over three weeks to include dual-aircraft jet blast deflector testing and catapult launches using a degraded catapult configuration to measure the effects of steam ingestion on the aircraft.
On 13 August 2011, the F-35 integrated test force completed jet blast deflector (JBD) testing at the Lakehurst facility, with a round of two-aircraft testing. F-35C test aircraft CF-1 along with an F/A-18E tested a combined JBD cooling panel configuration to assess the integration of F-35s in aircraft carrier launch operations. “We completed all of our JBD test points efficiently,” said Andrew Maack, government chief test engineer. “It was a great collaborative effort by all parties.” The government and industry team completed tests that measured temperatures, pressures, sound levels, velocities, and other environmental data. The combined JBD model is to enable carrier deck crews to operate all air wing aircraft, now including the F-35C, as operational tempo requires. Future carrier suitability testing is scheduled throughout 2011, including ongoing catapult testing and the start of arrestment testing in preparation for initial ship trials in 2013. On 18 November 2011, the U.S. Navy used its new Electromagnetic Aircraft Launch System (EMALS) to catapult an F-35C into the air for the first time.
The USN is dealing with the following issues in adapting their carriers to operate the F-35C.
- The F135 jet engine exceeds the weight capacity of traditional replenishment systems and generates more heat than previous engines.
- The F-35C's stealthy skin will require new repair techniques and extensive damage will require returning the aircraft to the factory for repairs.
- The F-35C uses volatile lithium-ion batteries and higher voltage systems than traditional fighters.
- The F-35C carries new weapons not previously used on carrier aircraft.
- The F-35C generates so much classified data that mission briefing rooms will require extra security.
Other versions
F-35I
The F-35I is an F-35A with Israeli modifications. A senior Israel Air Force official stated "the aircraft will be designated F-35I, as there will be unique Israeli features installed in them". Despite an initial refusal to allow such modifications, the U.S. has agreed to let Israel integrate its own electronic warfare systems into the aircraft’s built-in electronic suite. That would let Israel gradually add indigenously produced EW sensors and countermeasures once it receives its first squadron. In addition, a plug-and-play feature added to the main computer will allow for the use of Israeli electronics in an add-on fashion. Israel will be able to fit its own external jamming pod and plans to install its own air-to-air missiles and guided bombs in the F-35’s internal weapon bays. A contract was issued for this in 2012. Israeli pilots are scheduled to start training in F-35s in December 2016 with the first squadron activated about a year later.
Israel Aerospace Industries has considered playing a role in the development of a proposed two-seat F-35. An IAI executive stated, "There is a known demand for two seats not only from Israel but from other air forces. Advanced aircraft are usually two seats rather than single seats." IAI also plans to produce conformal fuel tanks to extend the range.
A senior IAF official has said that elements of the stealth on the F-35 may be overcome in 5 to 10 years, while the aircraft will be in service for 30 to 40 years, which is why Israel has insisted on the ability to install their own electronic warfare systems. “The basic F-35 design is OK. We can make do with adding integrated software.”
CF-35
The Canadian CF-35 is a proposed variant that would differ from the F-35A through the addition of a drag chute and an F-35B/C style refueling probe. Norway may also use the drag chute option, as they also have icy runways. The Norwegians have reported good results with using drag chutes on their current F-16 fleet and expect similar results with the F-35.
The alternative would be to adopt the F-35C for its probe refueling and lower landing speed, but the Parliamentary Budget Officer's report cited the F-35C's limited performance and payload as too high a price to pay. Although the heavier F-35C airframe does reduce the maximum G-level as compared to the F-35A, the F-35C will have both the largest internal fuel capacity and longest range out of the three F-35 variants, though it will be more expensive than the F-35A.
In 2012 it was revealed that the CF-35, if purchased, would use the same refueling system as the F-35A.
Operators
- United States Air Force
- United States Marine Corps
Specifications (F-35A)
Data from Lockheed Martin specifications, F-35 Program brief, F-35 JSF Statistics F-35 Program Status,
General characteristics
- Crew: 1
- Length: 51.4 ft (15.67 m)
- Wingspan: 35 ft (10.7 m)
- Height: 14.2 ft (4.33 m)
- Wing area: 460 ft² (42.7 m²)
- Empty weight: 29,300 lb (13,300 kg)
- Loaded weight: 49,540 lb (22,470 kg)
- Max. takeoff weight: 70,000 lb (31,800 kg)
- Powerplant: 1 × Pratt & Whitney F135 afterburning turbofan
- Dry thrust: 28,000 lbf (125 kN)
- Thrust with afterburner: 43,000 lbf (191 kN)
- Internal fuel capacity: 18,480 lb (8,382 kg)
Performance
- Maximum speed: Mach 1.6+ (1,200 mph, 1,930 km/h) (tested to Mach 1.61)
- Range: 1,200 nmi (2,220 km) on internal fuel
- Combat radius: 584 nmi (1,080 km) on internal fuel
- Service ceiling: 60,000 ft (18,288 m) (tested to 43,000 ft)
- Rate of climb: classified (not publicly available)
- Wing loading: 107.7 lb/ft² (446 kg/m²; 526 kg/m² loaded)
- Thrust/weight:
- With full fuel: 0.87
- With 50% fuel: 1.07
- Max g-limits: 9 g (4.6 g in a sustained turn)
Armament
- Guns: 1 × General Dynamics GAU-22/A Equalizer 25 mm (0.984 in) 4-barreled gatling cannon, internally mounted with 180 rounds
- Hardpoints: 6 × external pylons on wings with a capacity of 15,000 lb (6,800 kg) and two internal bays with two pylons each for a total weapons payload of 18,000 lb (8,100 kg) and provisions to carry combinations of:
- Missiles:
- Air-to-air missiles:
- AIM-120 AMRAAM
- AIM-9X Sidewinder
- IRIS-T
- MBDA Meteor (pending further funding)
- Air-to-surface missiles:
- AGM-88 AARGM
- AGM-158 JASSM
- Brimstone missile / MBDA SPEAR
- Joint Air-to-Ground Missile
- Storm Shadow missile
- SOM
- Anti-ship missiles:
- JSM
- LRASM
- Air-to-air missiles:
- Bombs:
- Mark 84, Mark 83 and Mark 82 GP bombs
- Mk.20 Rockeye II cluster bomb
- Wind Corrected Munitions Dispenser capable
- Paveway series laser-guided bombs
- Small Diameter Bomb (SDB)
- JDAM series
- B61 nuclear bomb
- AGM-154 JSOW
- Missiles:
Avionics
- Northrop Grumman Electronic Systems AN/APG-81 AESA radar
- Lockheed Martin AAQ-40 E/O Targeting System (EOTS)
- Northrop Grumman Electronic Systems AN/AAQ-37 Distributed Aperture System (DAS) missile warning system
- BAE Systems AN/ASQ-239 (Barracuda) electronic warfare system
- Harris Corporation Multifunction Advanced Data Link (MADL) communication system
F-35A CTOL |
F-35B STOVL |
F-35C CATOBAR |
|
---|---|---|---|
Length | 51.4 ft (15.7 m) | 51.3 ft (15.6 m) | 51.5 ft (15.7 m) |
Wingspan | 35 ft (10.7 m) | 35 ft (10.7 m) | 43 ft (13.1 m) |
Wing Area | 460 ft² (42.7 m²) | 460 ft² (42.7 m²) | 668 ft² (62.1 m²) |
Empty weight | 29,300 lb (13,300 kg) | 32,300 lb (14,700 kg) | 34,800 lb (15,800 kg) |
Internal fuel | 18,250 lb (8,280 kg) | 13,500 lb (6,125 kg) | 19,750 lb (8,860 kg) |
Max takeoff weight | 70,000 lb class (31,800 kg) | 60,000 lb class (27,300 kg) | 70,000 lb class (31,800 kg) |
Range | 1,200 nmi (2,220 km) | 900 nmi (1,670 km) | 1,400 nmi (2,520 km) |
Combat radius on internal fuel |
584 nmi (1,082 km) | 469 nmi (869 km) | 615 nmi (1,141 km) |
Thrust/weight • full fuel: • 50% fuel: |
0.87 1.07 |
0.90 1.04 |
0.75 0.91 |